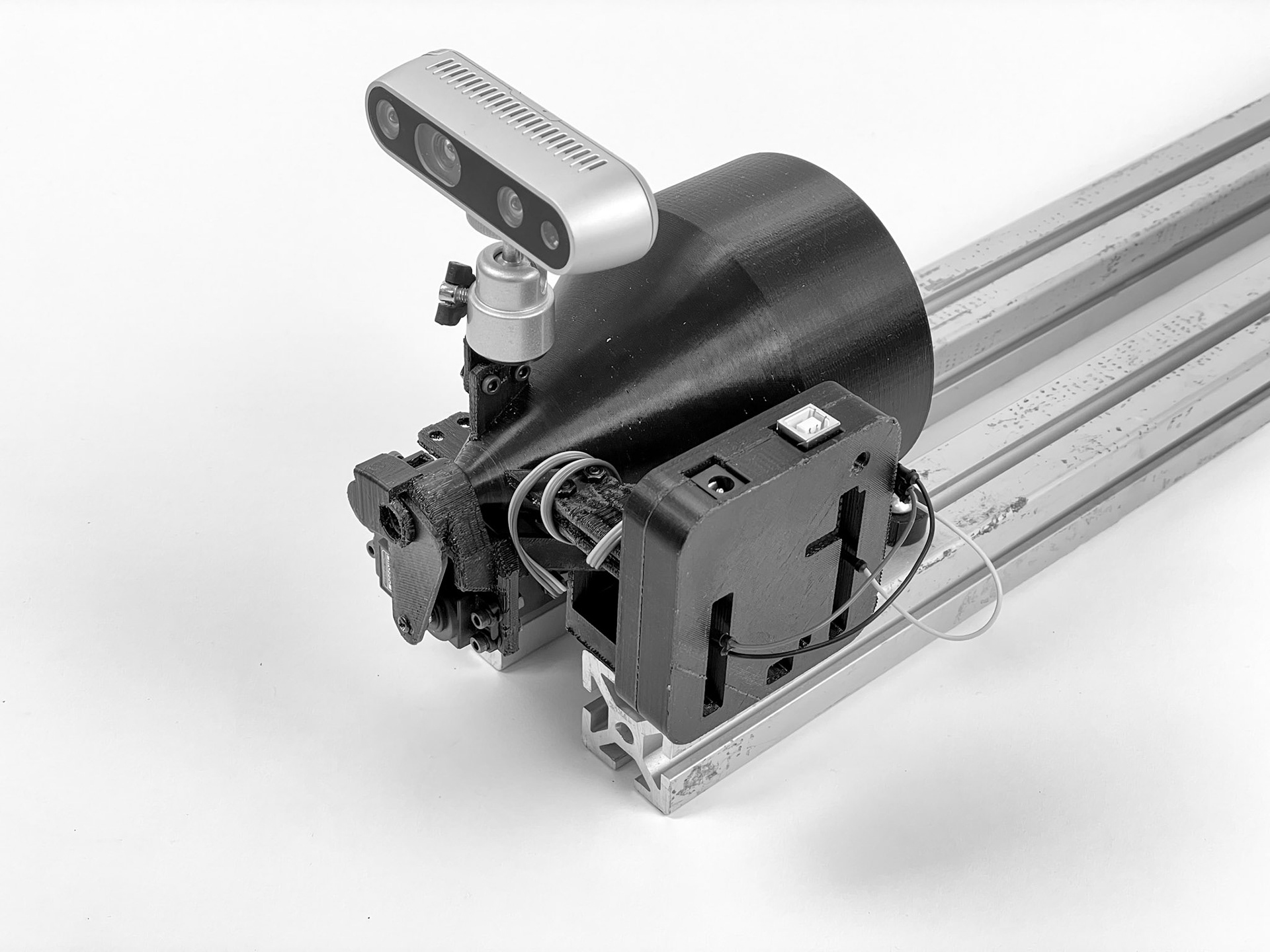
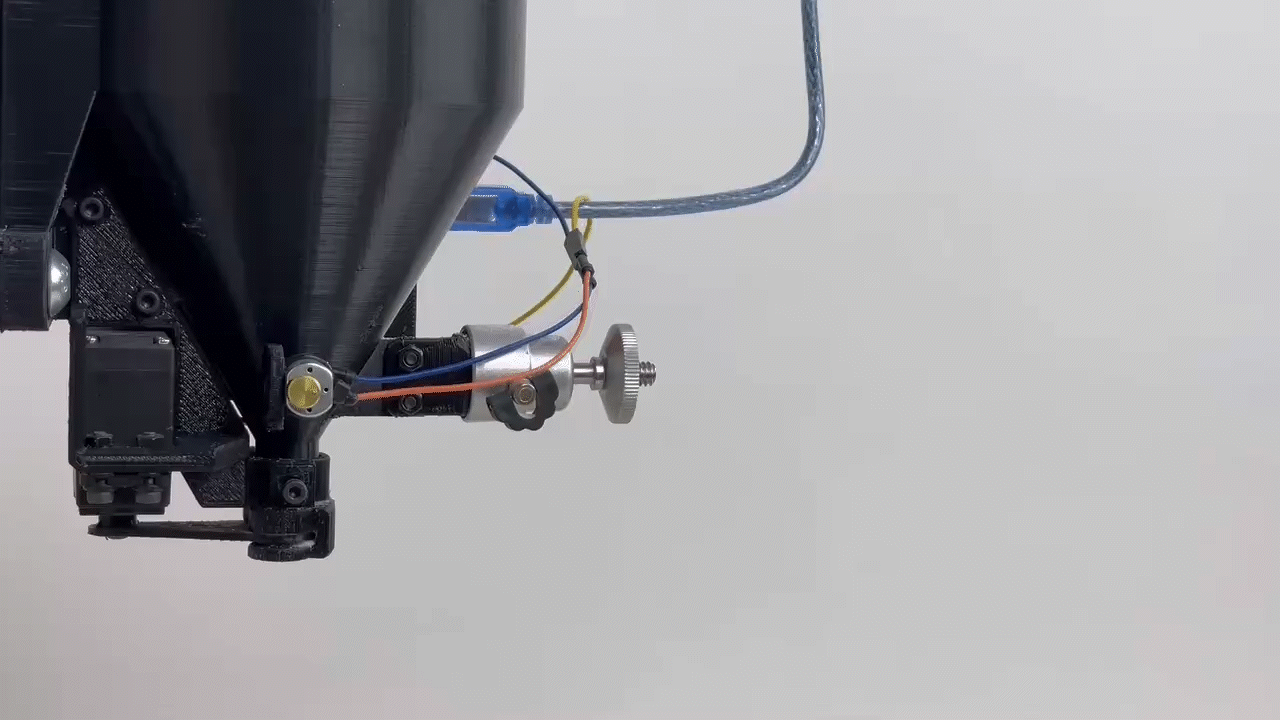
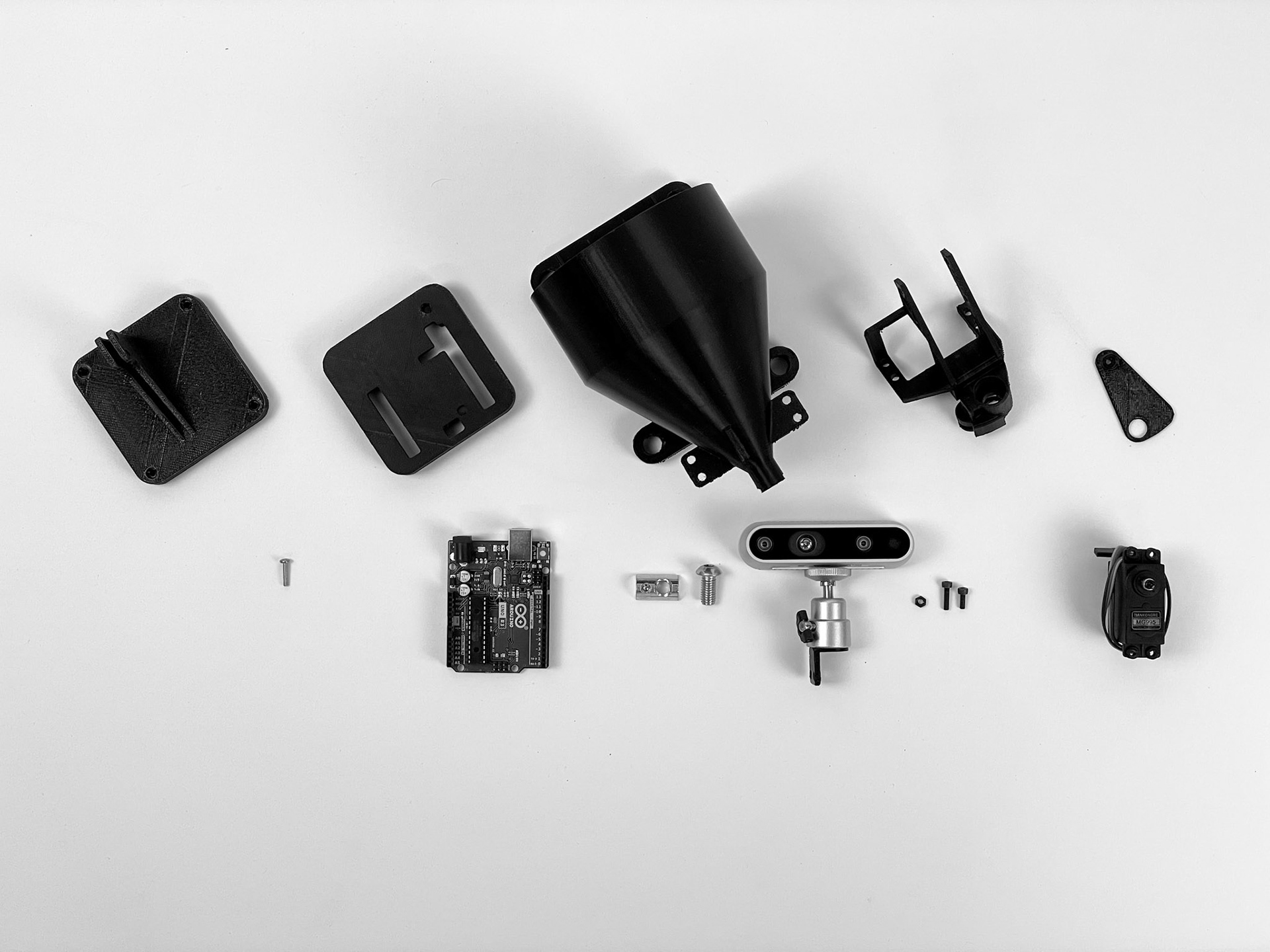
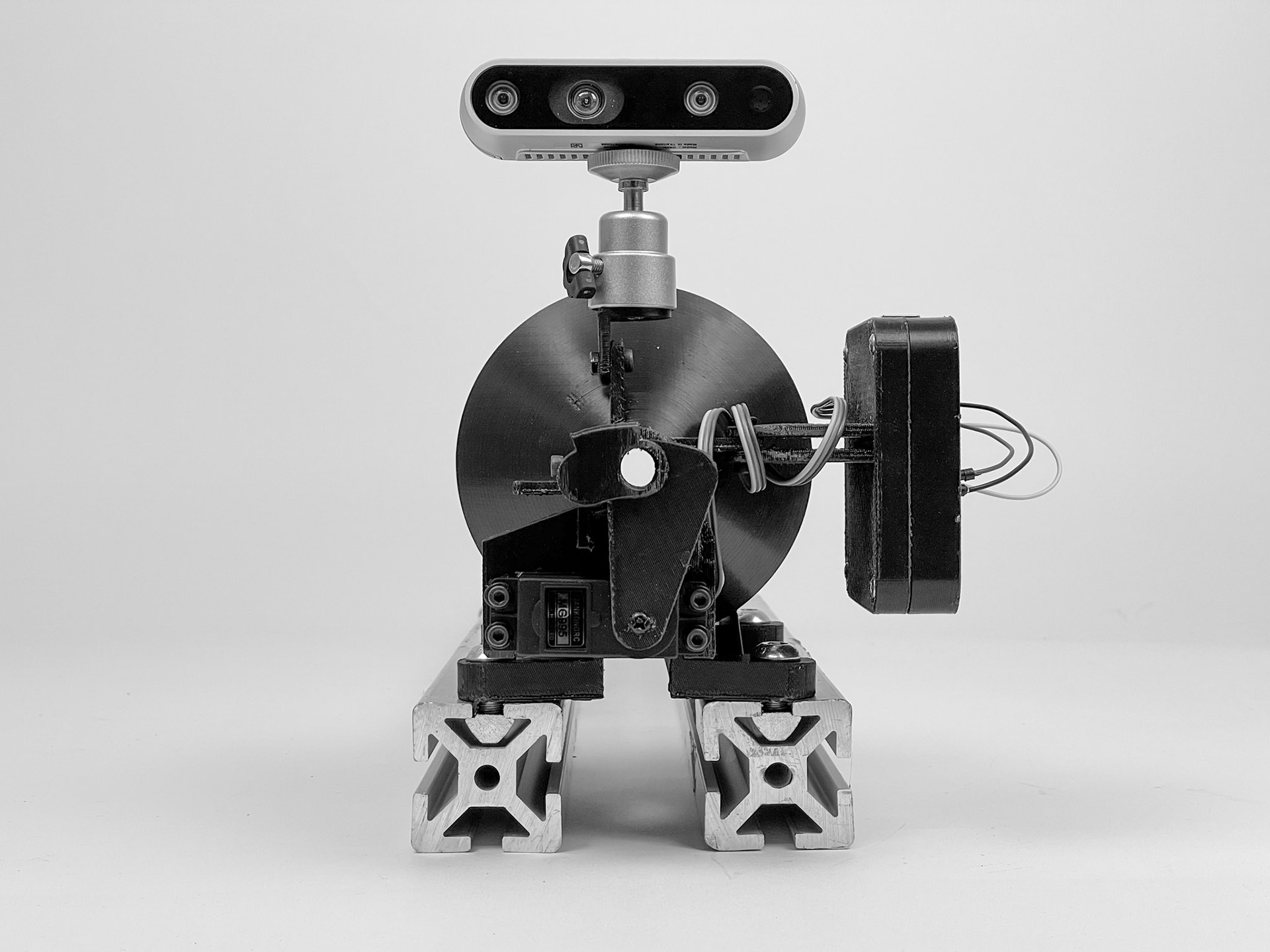
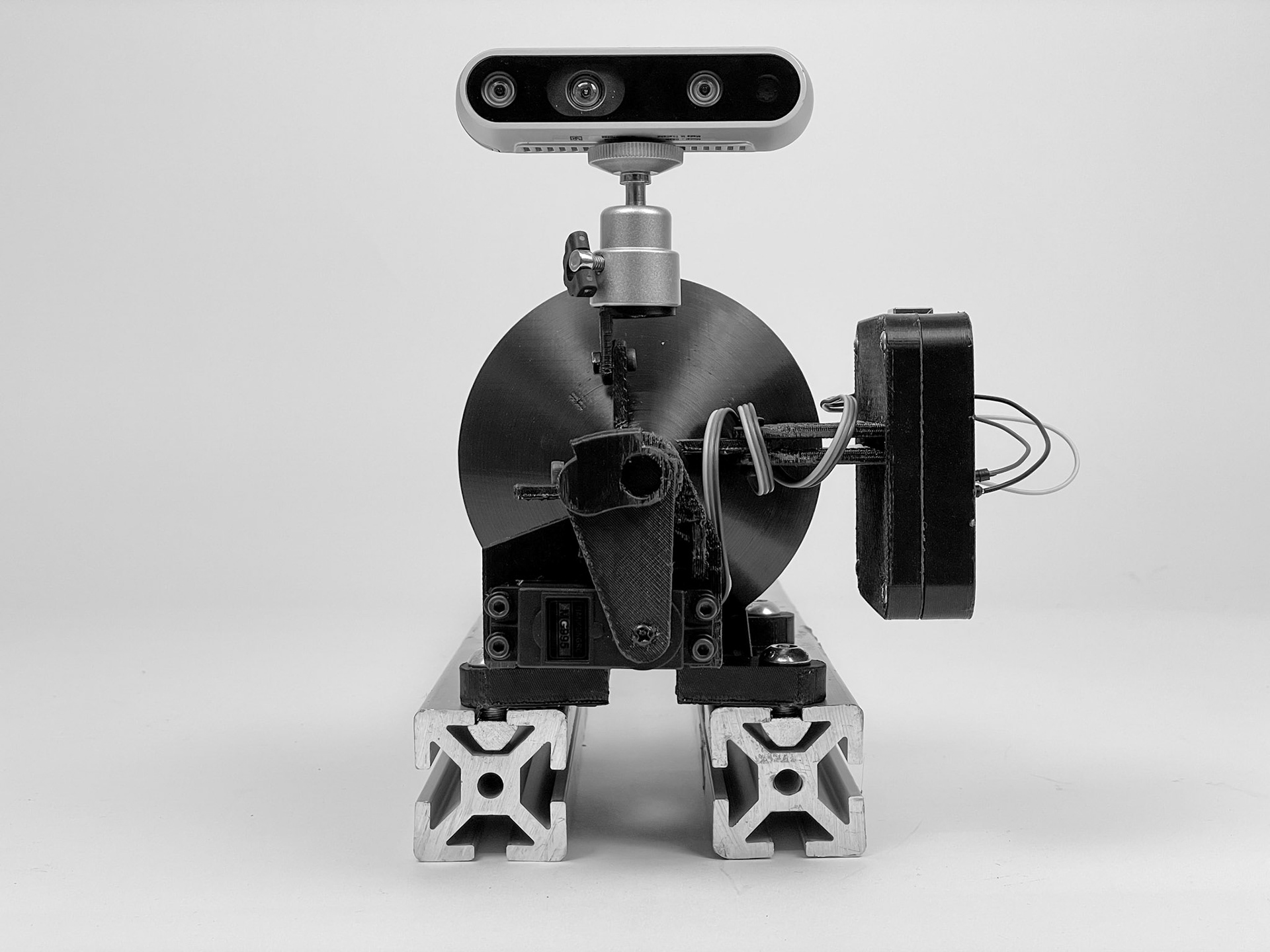
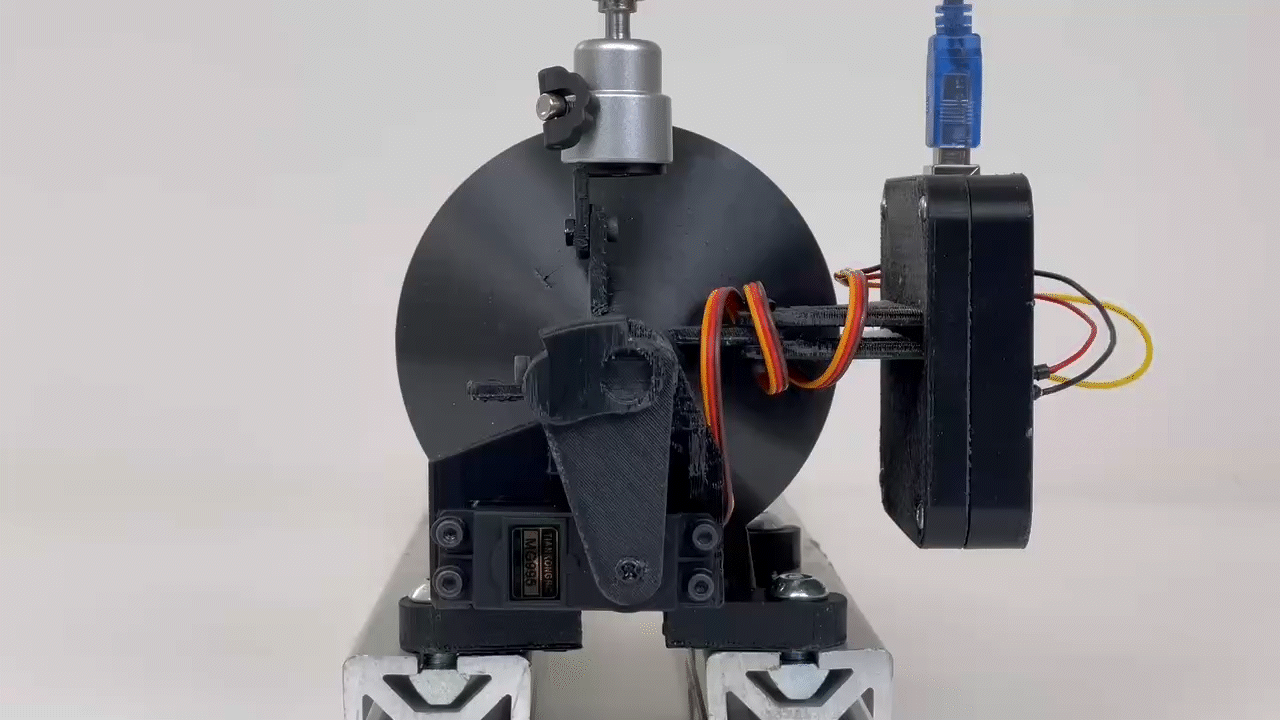
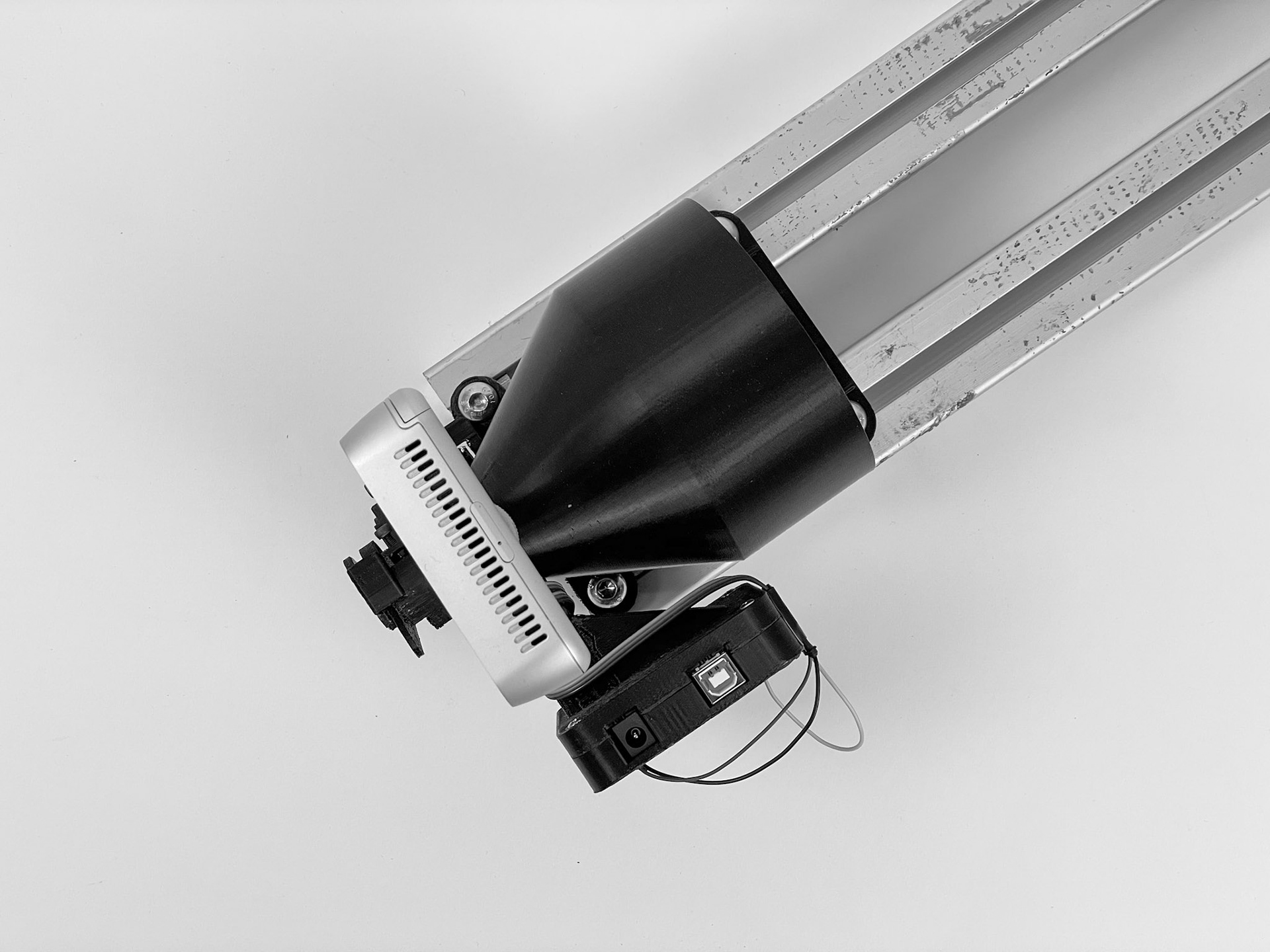
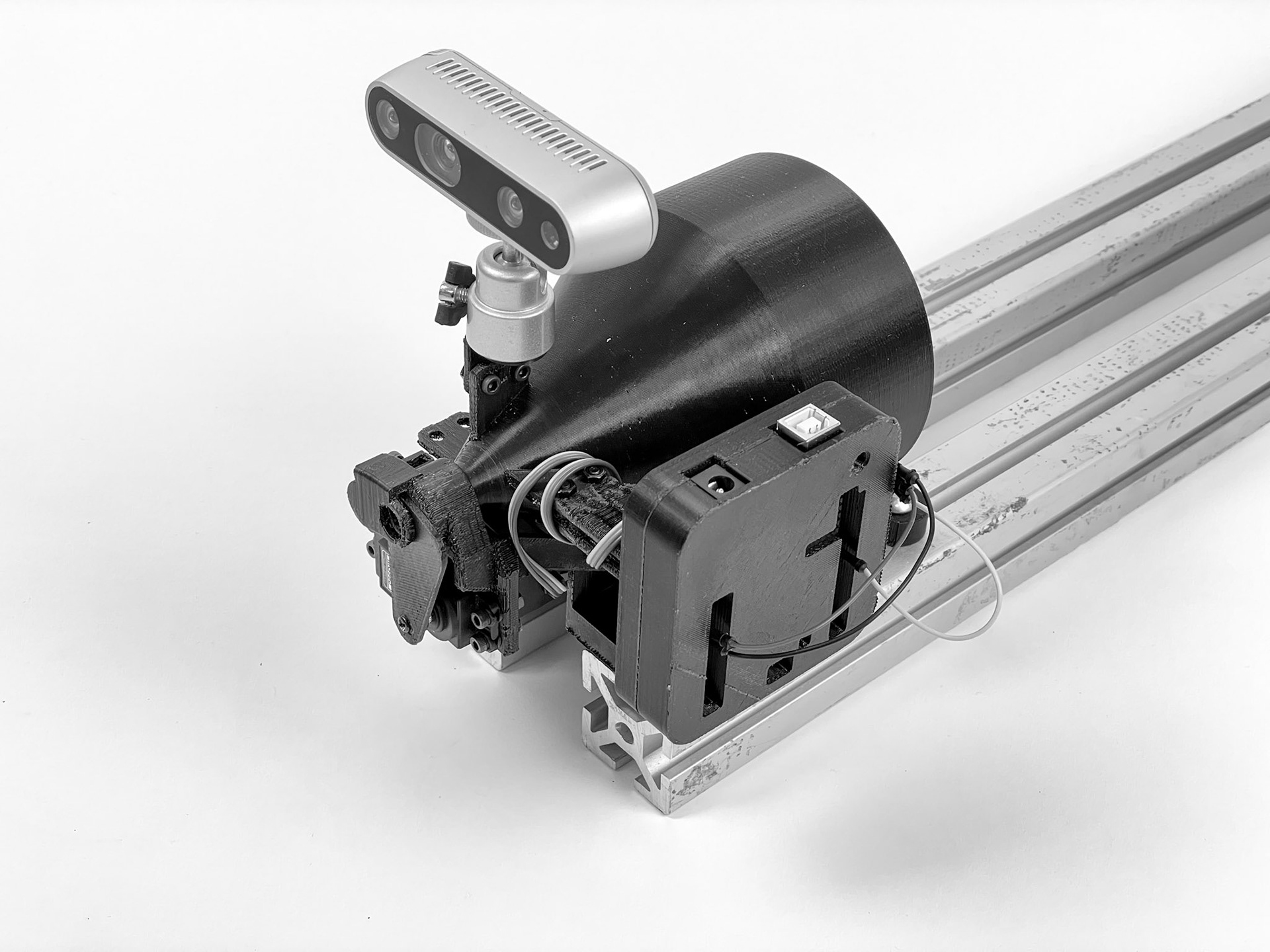
1. Hypothesized sand formation as predictable support for 3D printing clay in the manufacturing process.
2. To control sand formation as a supporting material, we designed an end effector to deposit sand.
3. With a sand extrusion controlled by a valving nozzle and smoothened by a vibrating motor, sand accumulates as a prediction.
4. This sand depositing method is regarded as an integrated fabrication system that can be controlled by ABB RobotStudio.
5. To prevent sand flow inaccuracy due to the height and pressure variety, a filter engaged as a sand decompressor.
2. To control sand formation as a supporting material, we designed an end effector to deposit sand.
3. With a sand extrusion controlled by a valving nozzle and smoothened by a vibrating motor, sand accumulates as a prediction.
4. This sand depositing method is regarded as an integrated fabrication system that can be controlled by ABB RobotStudio.
5. To prevent sand flow inaccuracy due to the height and pressure variety, a filter engaged as a sand decompressor.
In order to get additional control of sand deposition, we designed a custom end-of-arm tool for the ABB IRB4600 industrial robotic arm. Once deposited robotically by our custom tool, the sand accumulated on our formwork as predicted in the 3D CAD simulation. The tool is equipped with a valving nozzle, controlled in real-time by an Arduino UNO board, a vibrating motor attachment, and a circuit board as a cerebellum. Sandfall is determined by the robots input/output modules - sending high and low signals to the Arduino UNO board, turning the valving nozzle on and off, respectively. Utilizing the cerebellum-like method, ABB RobotStudio could perform as a integrated fabrication system that controls both robotic path planning as well as sand deposition. After the sand is deposited, the end-of-arm tool we scanned the sand 3D topology with depth camera Realsense D435 as an input of tool path planning script in Grasshopper. The script would then plan out a feasible tool path for the next layer of 3D clay printing and sand formation. An integrated fabrication system was introduced in which we packed almost every experimental variable, such as extruding time and extruding speed into one system. The design improved the efficiency when prooving our hypothesis.
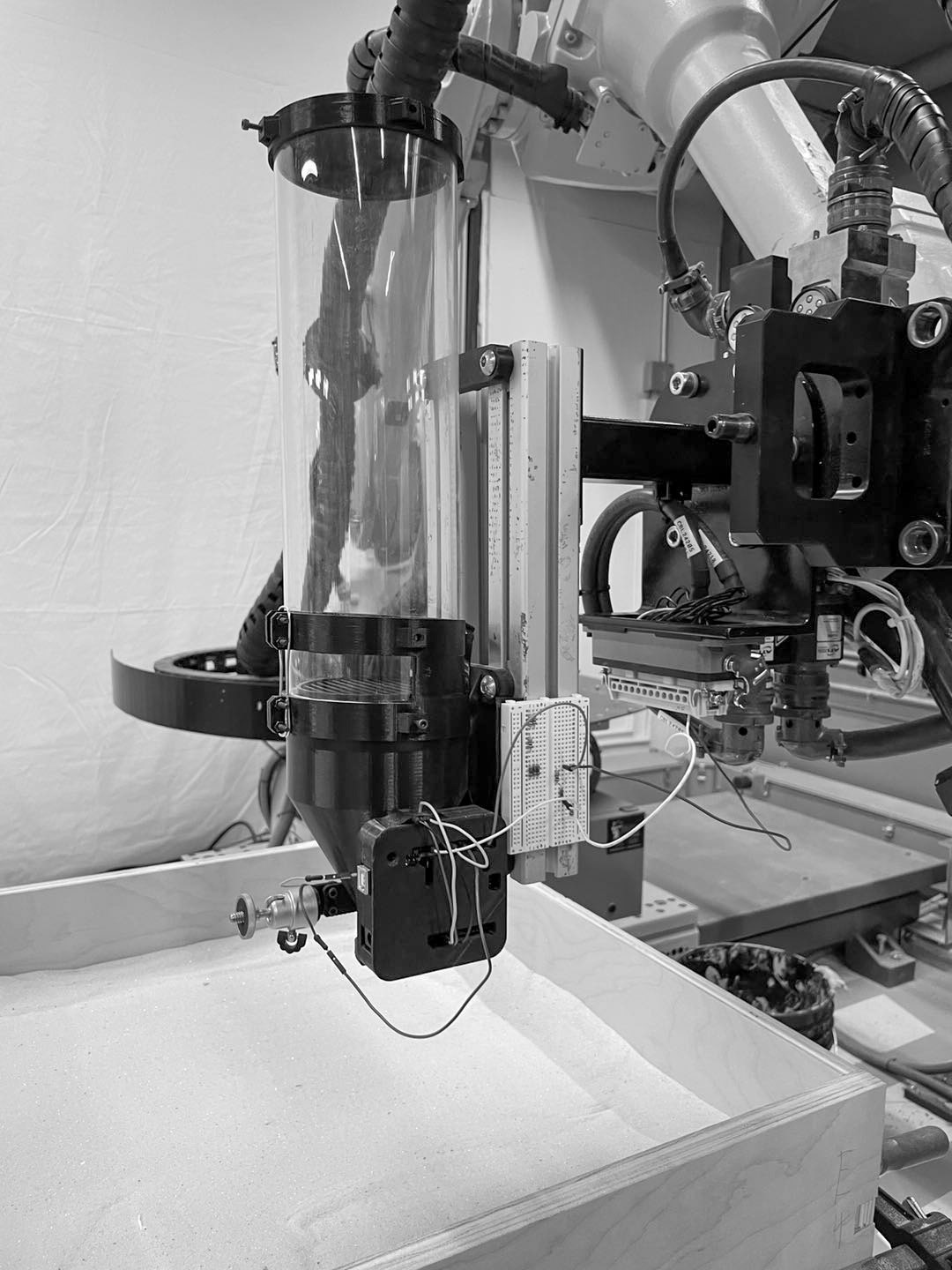
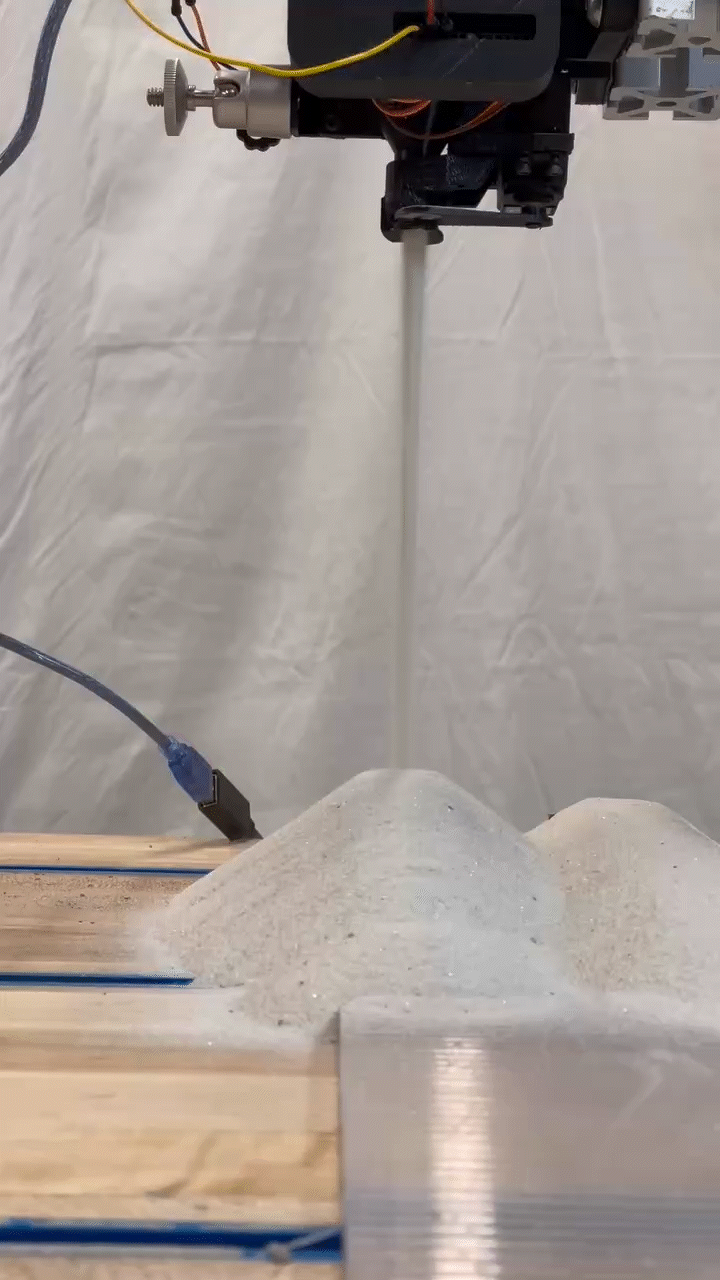
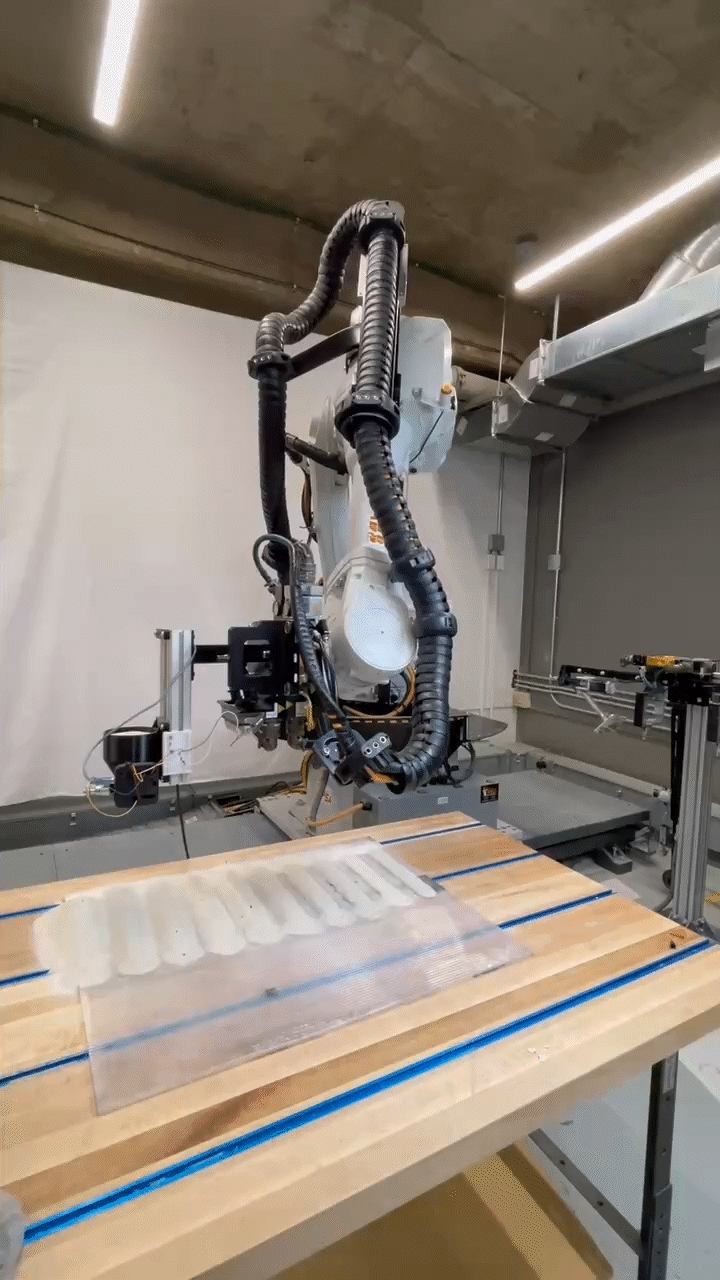
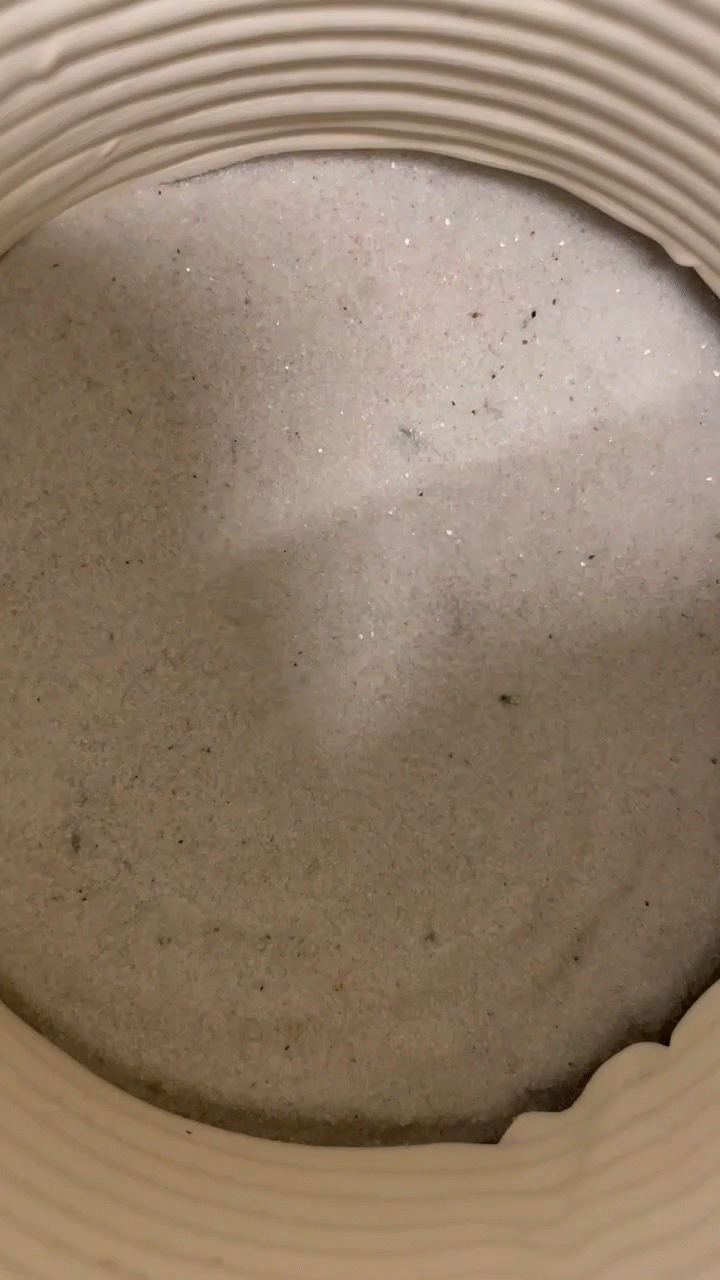
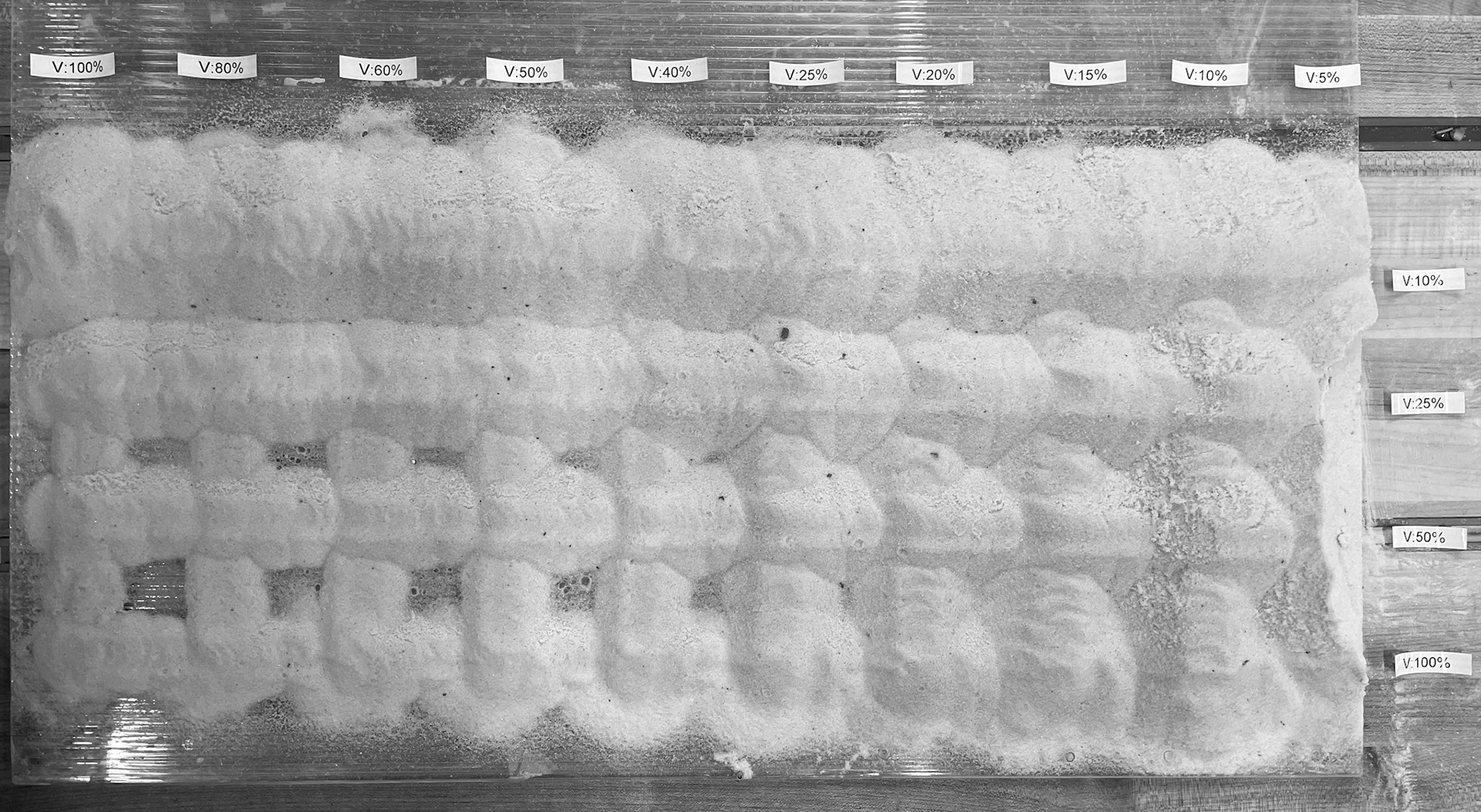
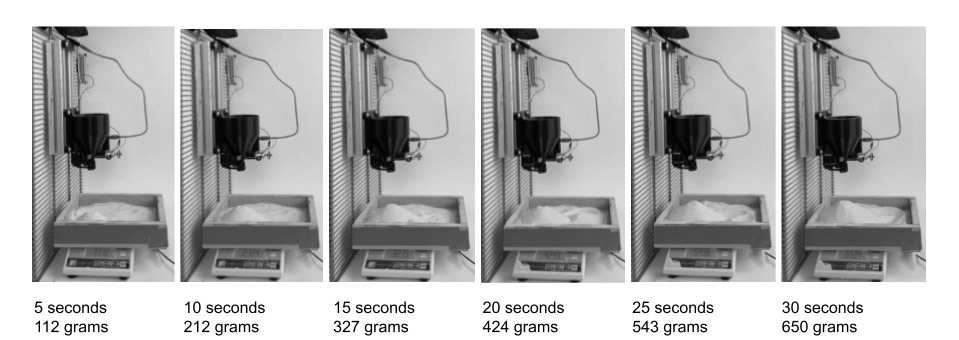
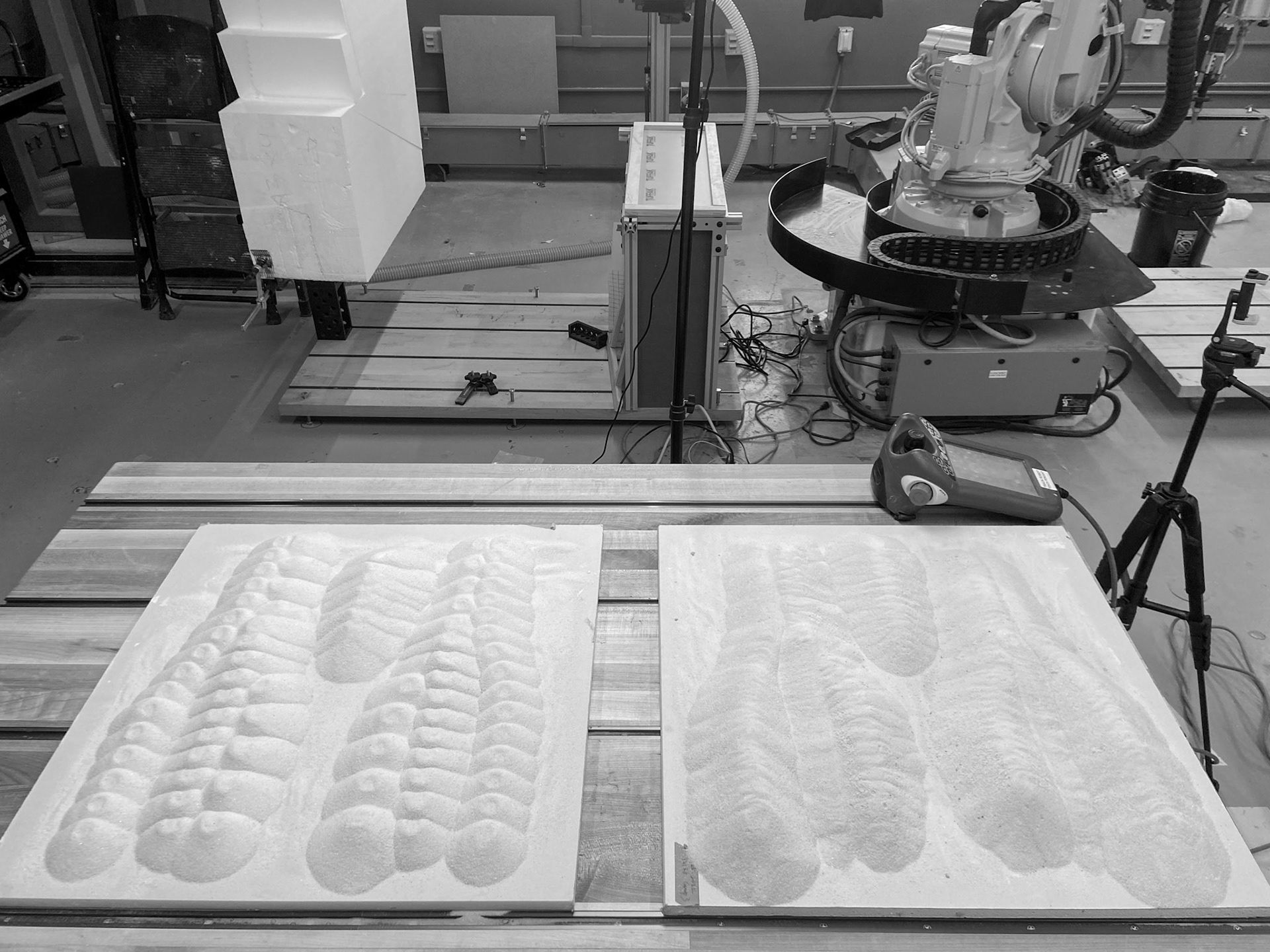
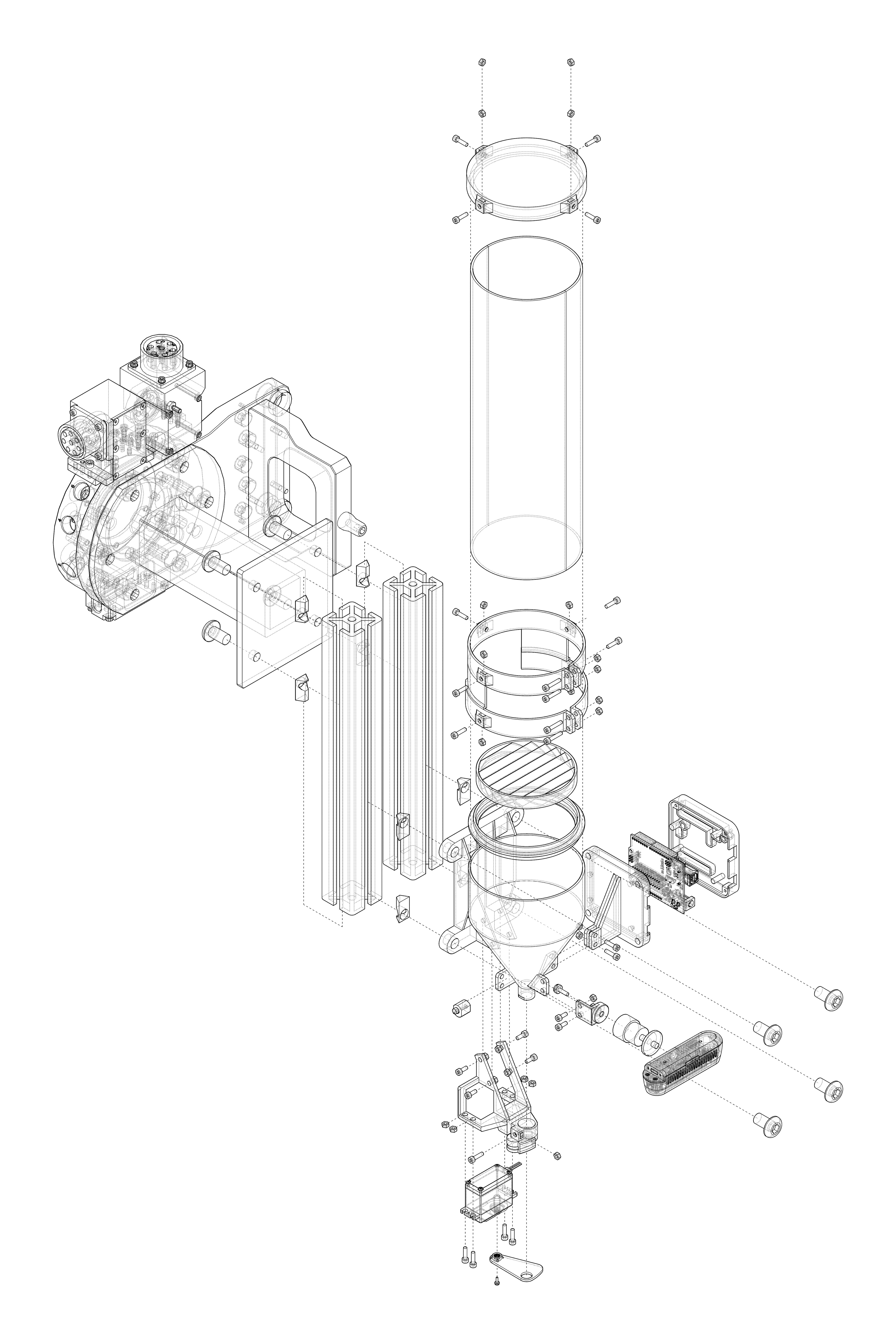
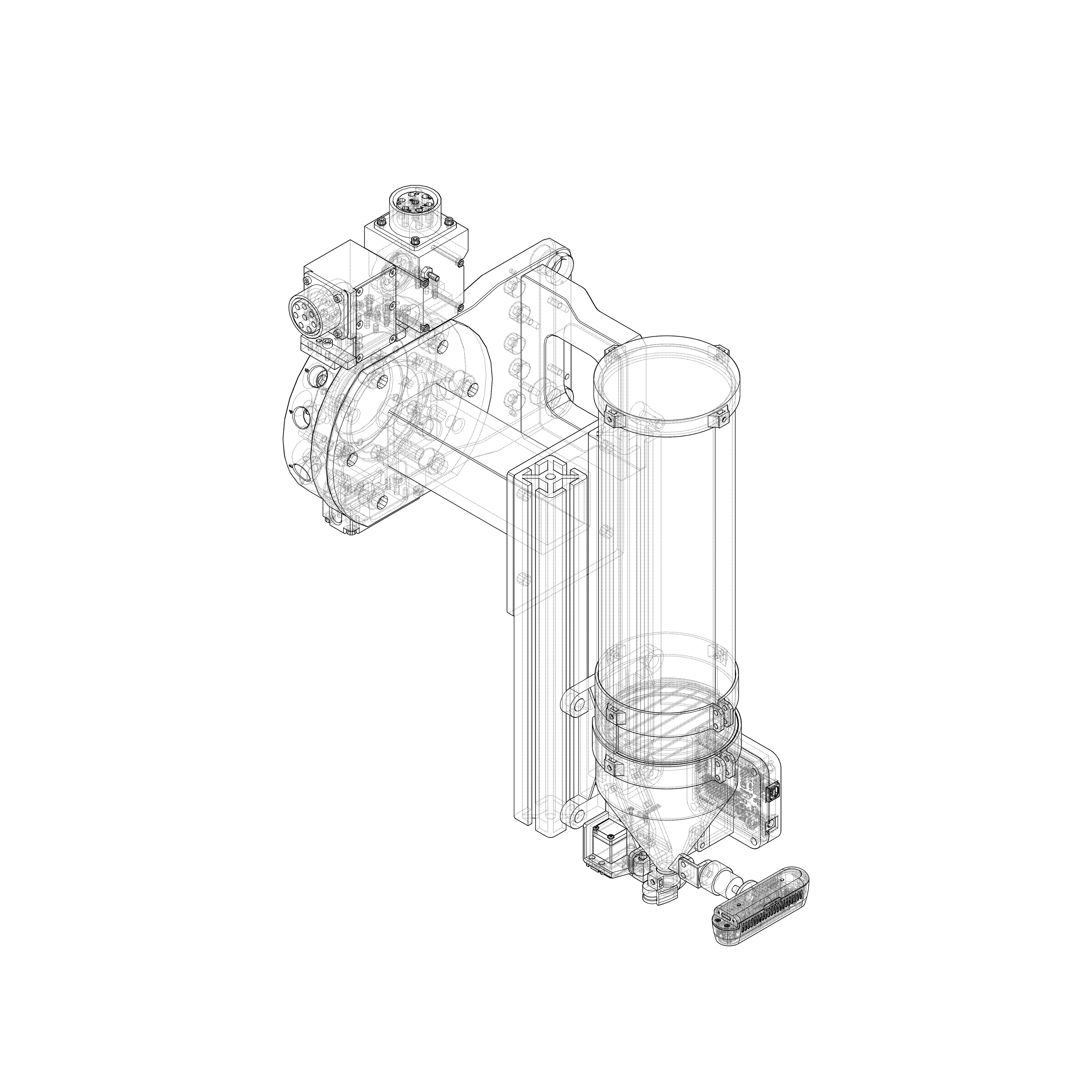
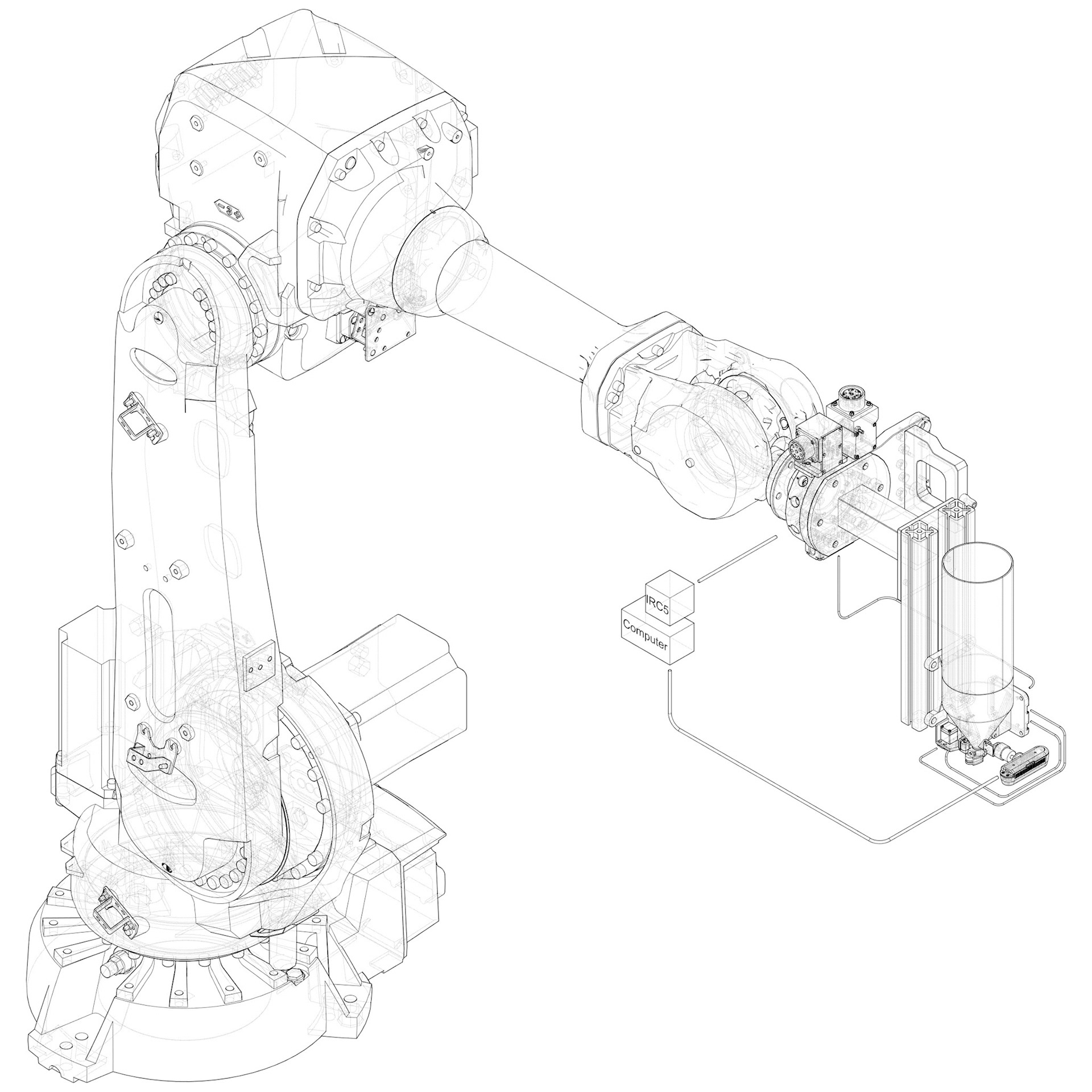
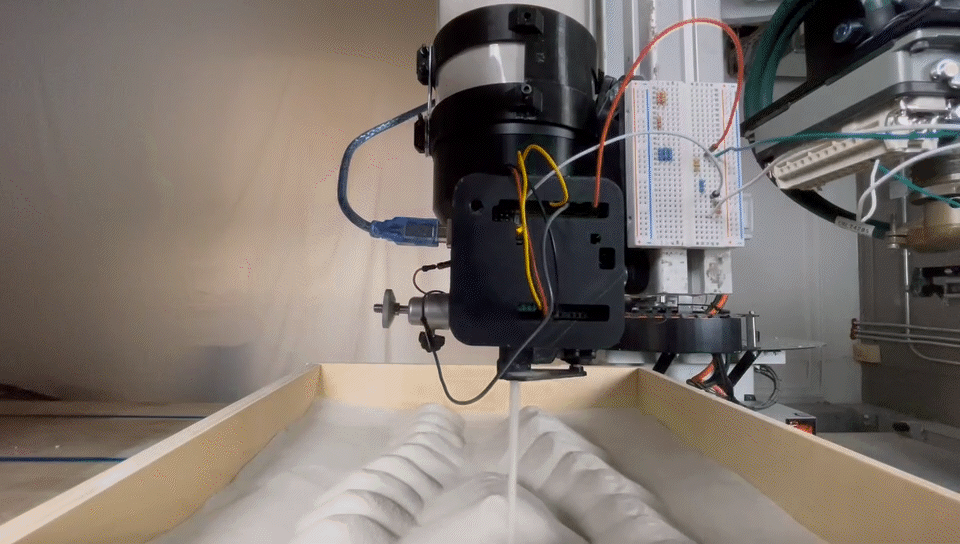
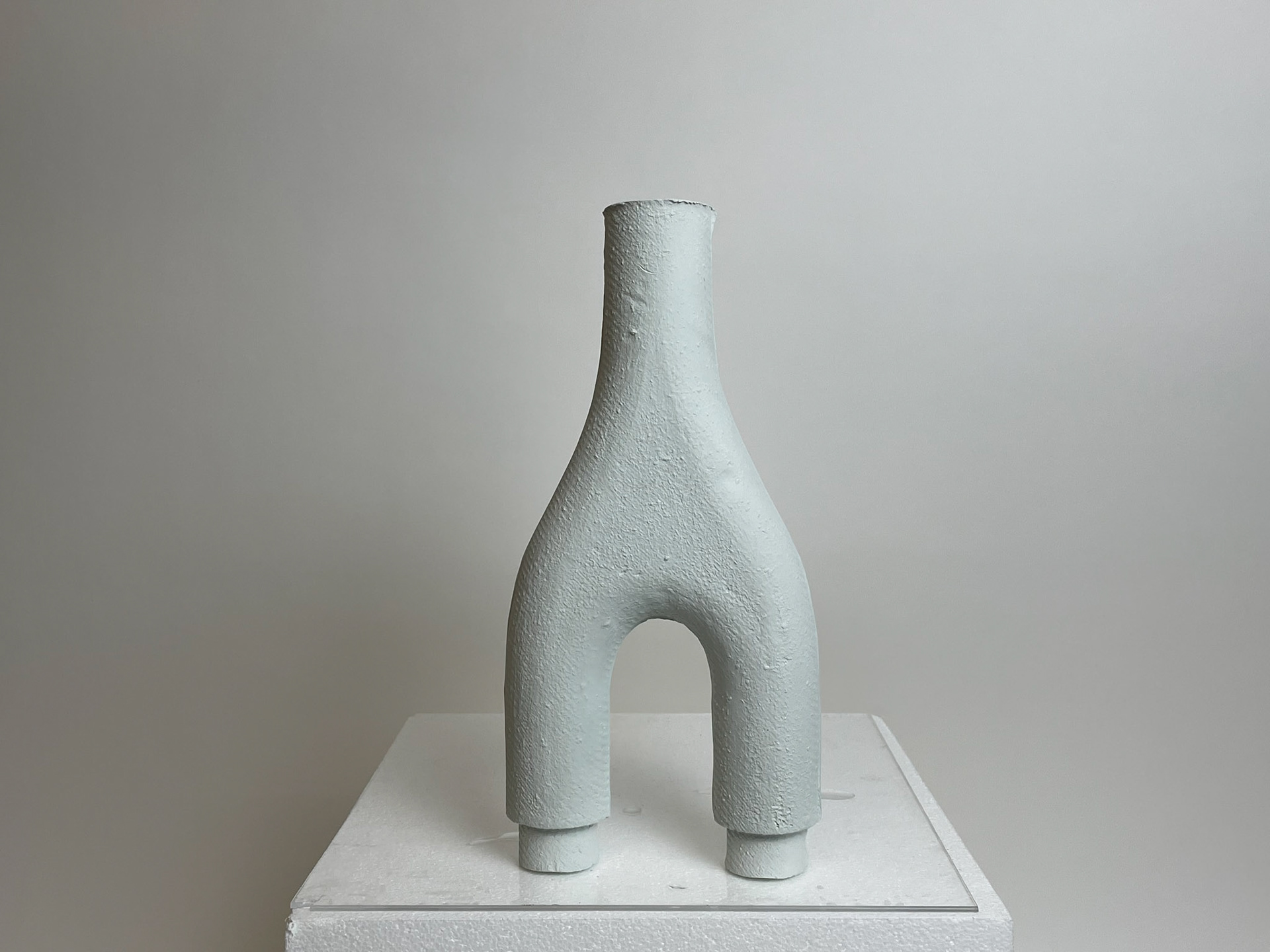
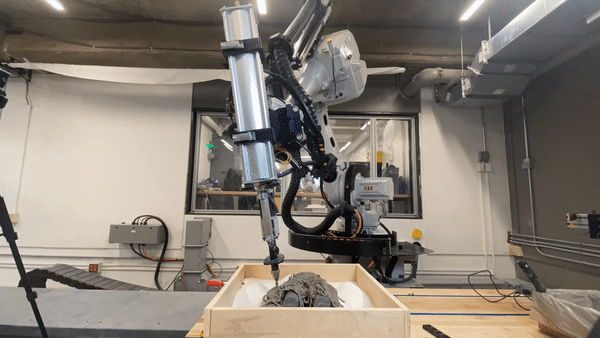
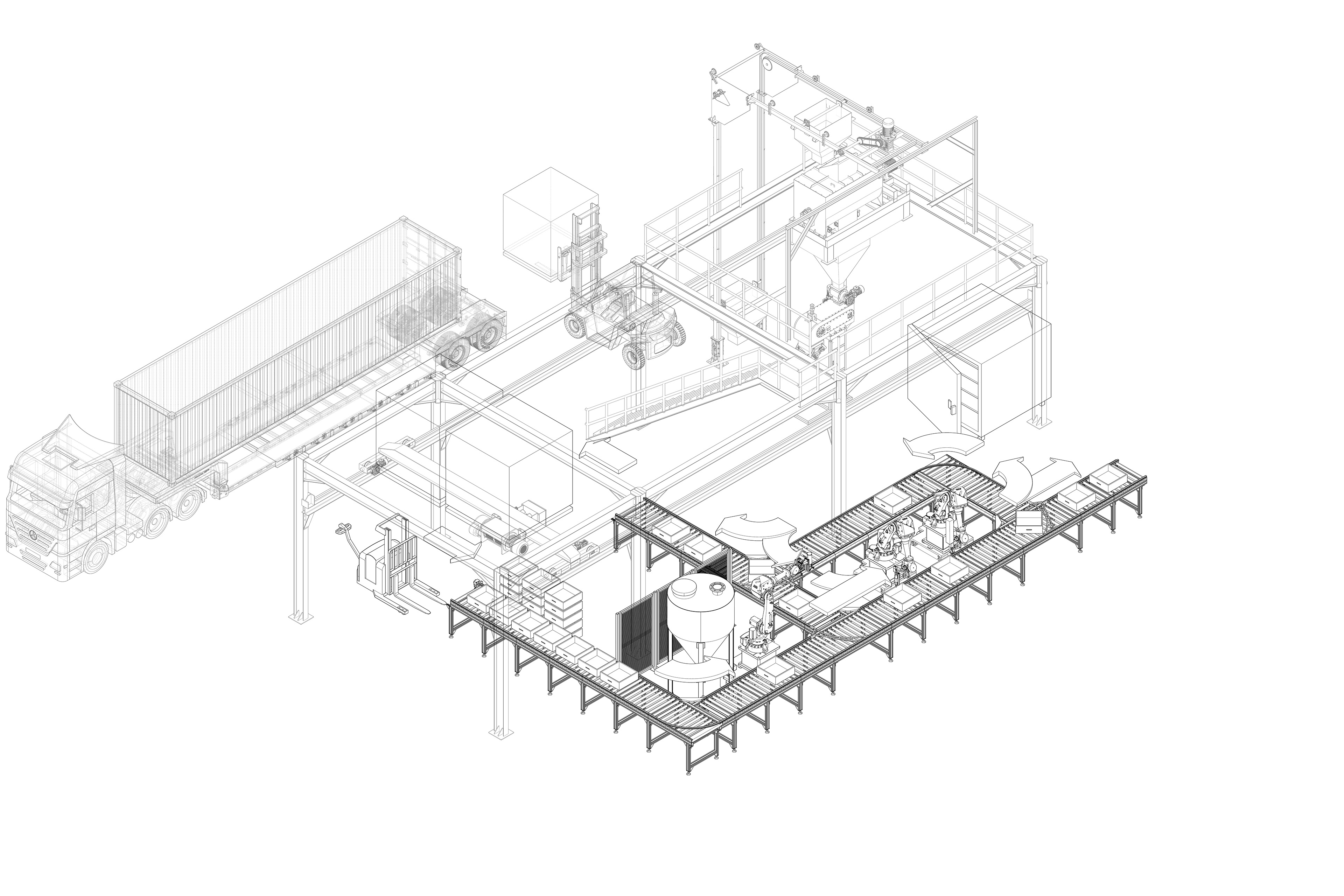
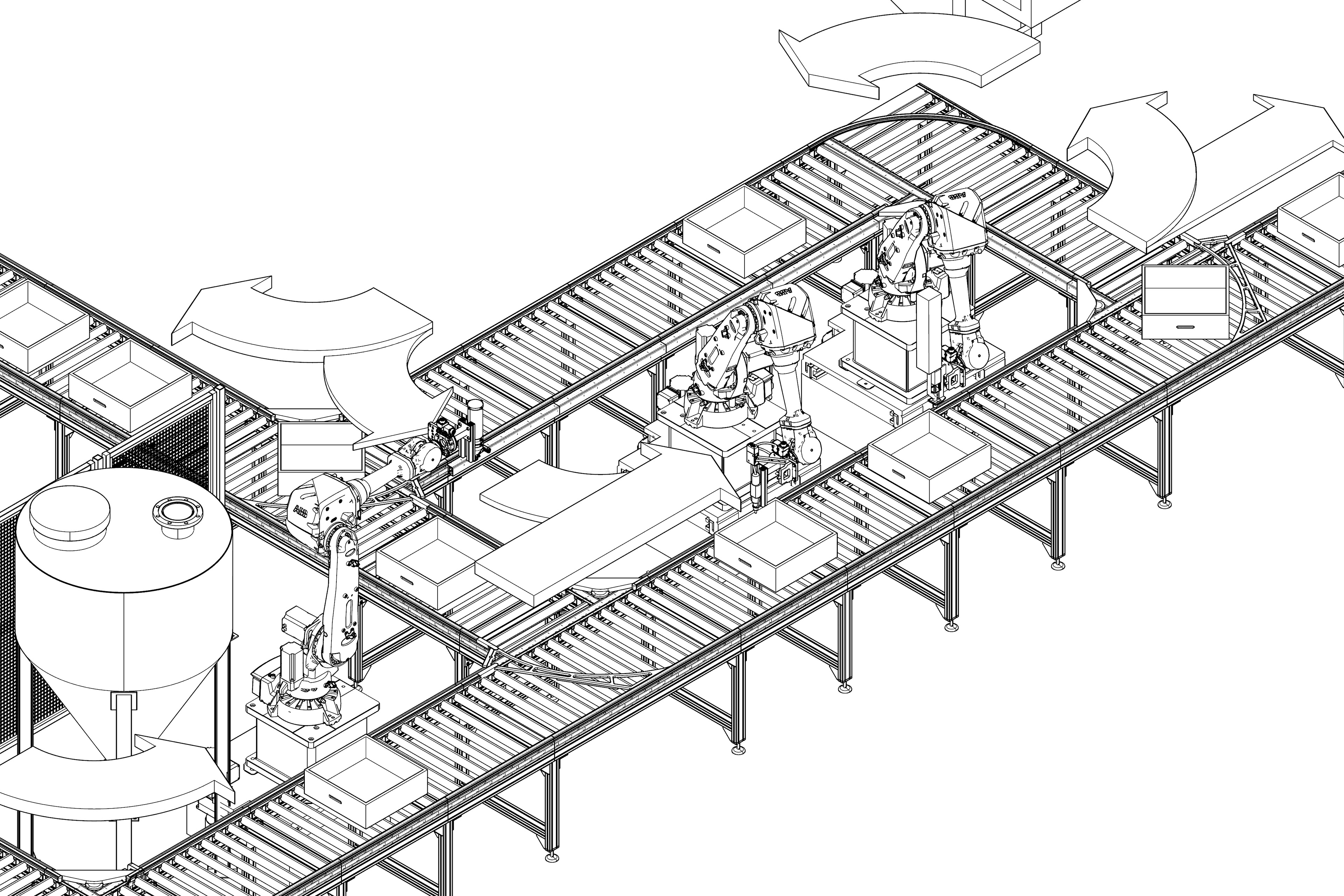
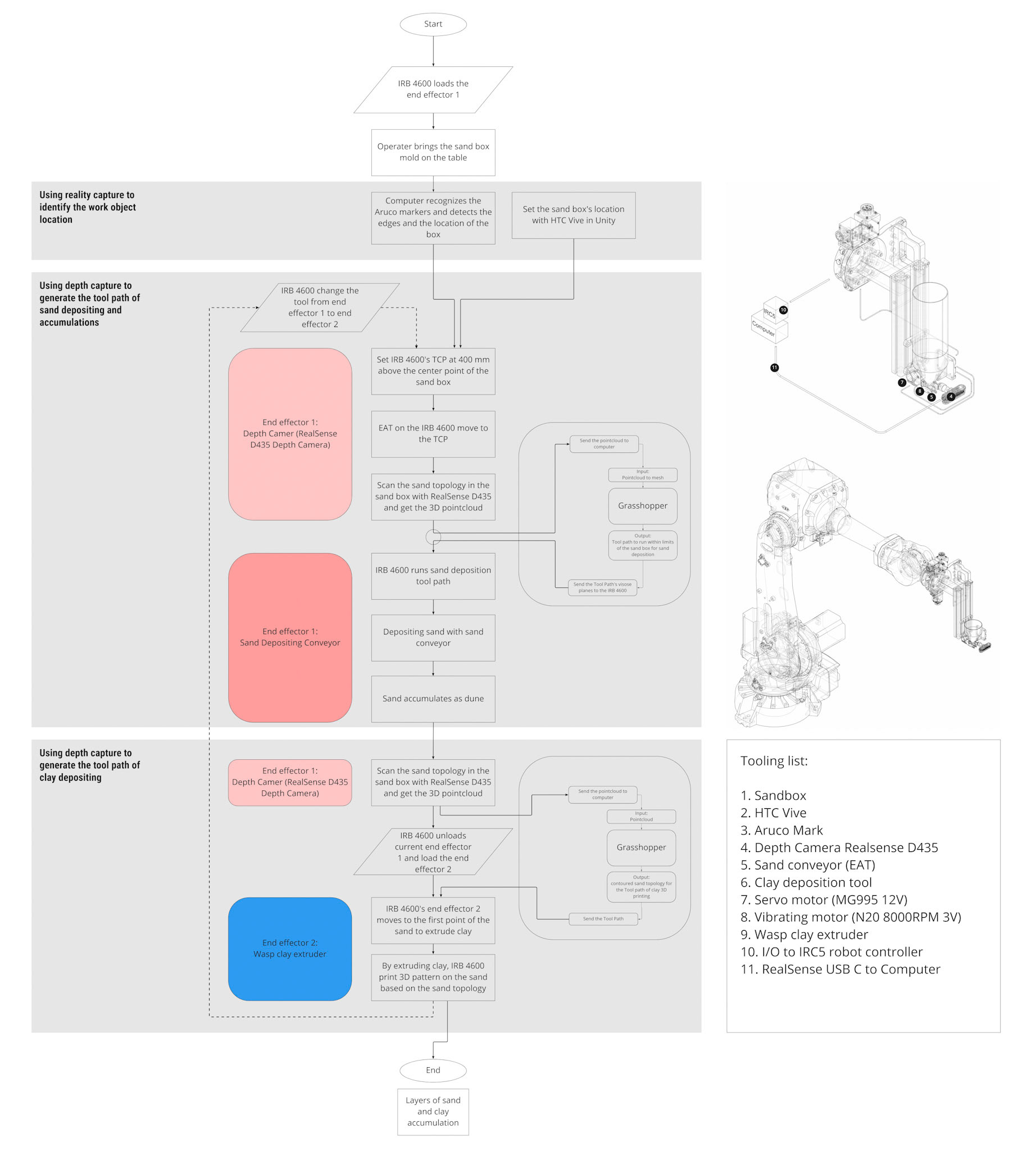
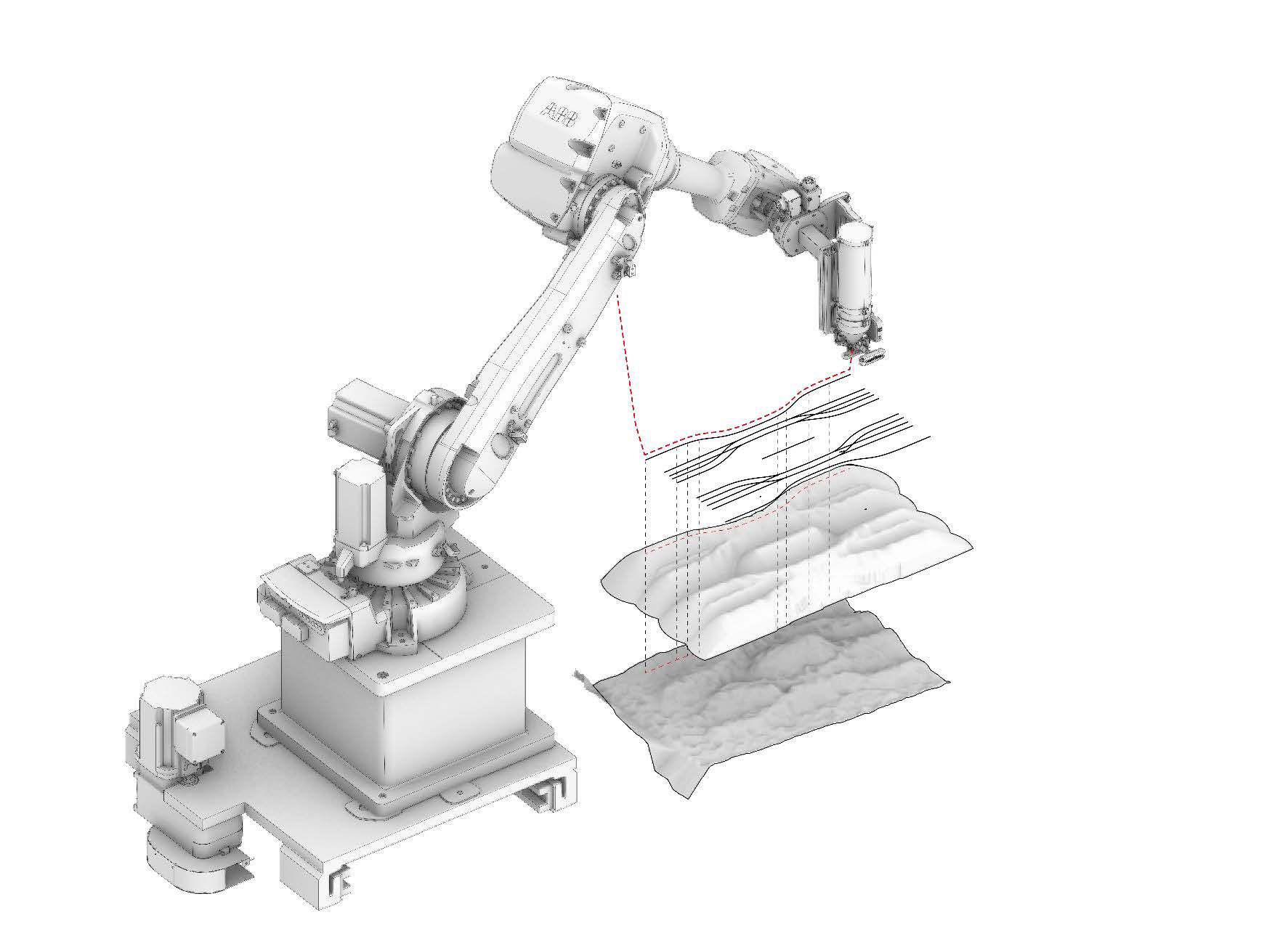
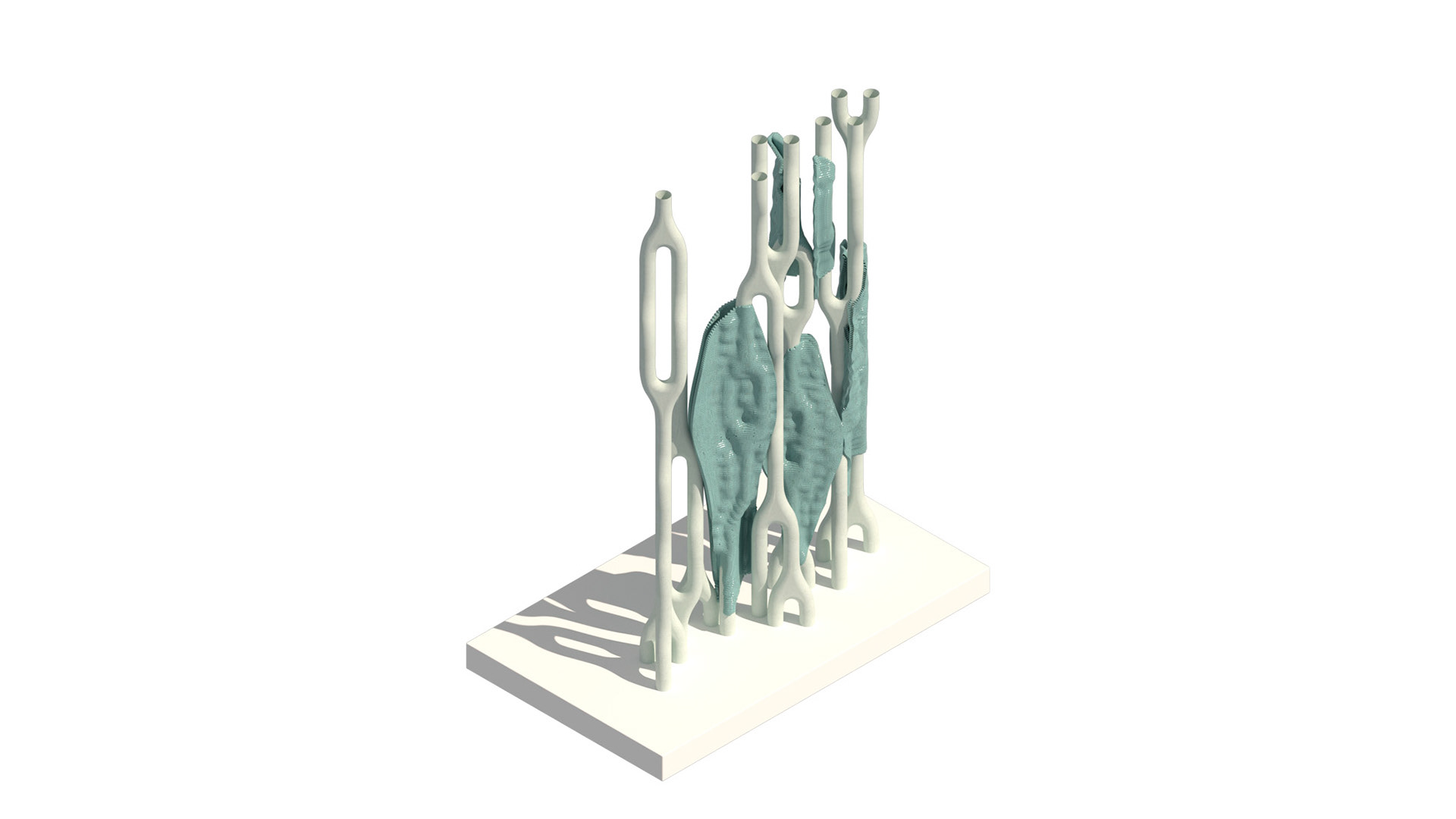
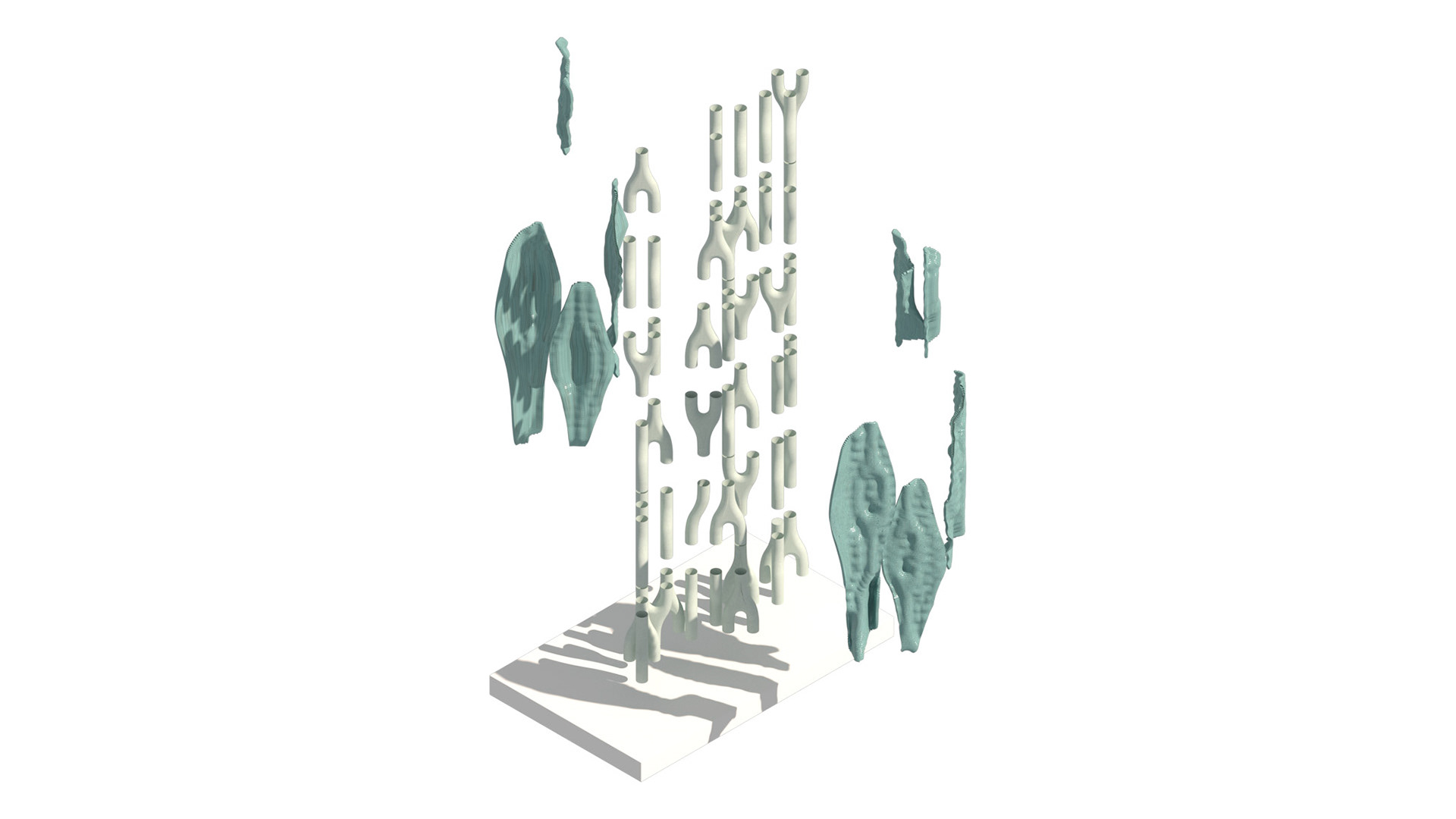
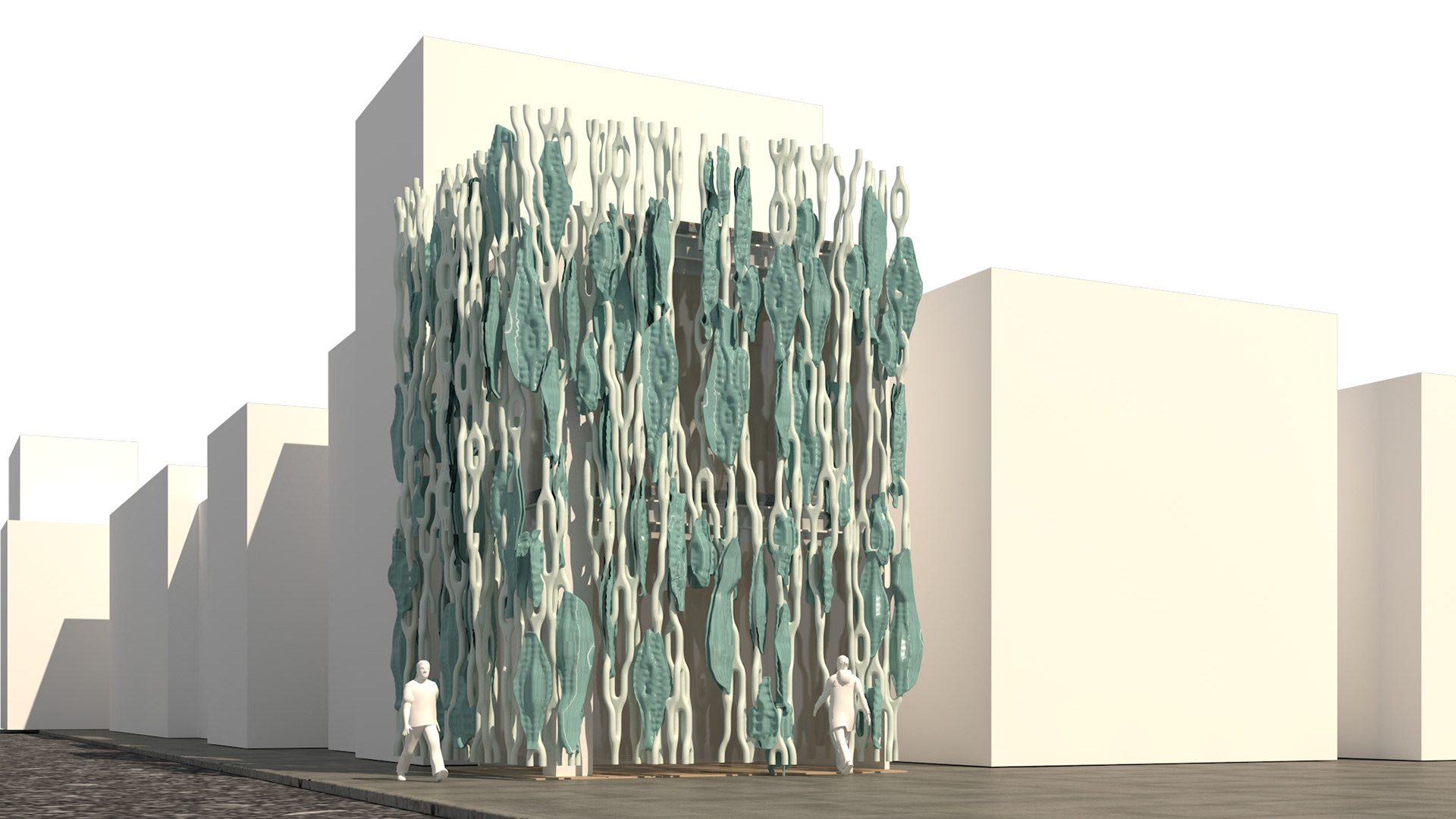