INSPIRATION:
By implementing the innovative low-carbon concrete material, optimizing essential structural forms, and adopting the robotics fabrication system, the 3D printed urban blocks can reduce 30% of overall material waste and increase 80% manufacturing efficiency to achieve the most sustainable and efficient adaptability. The team offers more freedom to bespoke forms and advanced parametric designs by utilizing the technology.
UNIQUE PROPERTIES / PROJECT DESCRIPTION:
This urban furniture prototype can easily adapt to any built environment. Urban Blocks’form can be positioned and combined for different purposes with structural algorithm optimization analysis—single bench, double-side bench, sofas, planters, and variations in-between. The geometry and scale of the mobile units permit easy assemblies to fit the human body. This design aims to empower the communities by prefabricating urban blocks and to open up countless possibilities to populate our public spaces.
OPERATION / FLOW / INTERACTION:
The units are made in factories using sustainable 3D printed concrete with an autonomous robotics fabrication system and transported to sites. People can position them and make different compositions from the blocks to create adaptive urban furniture and landscape elements.
PRODUCTION / REALIZATION TECHNOLOGY:
Prefab Units, Low-Carbon 3D Printed Concrete, Autonomous Manufacture, Robotics fabrication, Modular Design, Bespoke Parametric Design
SPECIFICATIONS / TECHNICAL PROPERTIES:
For each block: 600mm x 750mm x 600mm (being used). When being manufactured/transported, the orientation of the object will be 600mm x 600mm x 750mm to be printed by robots.
CHALLENGE:
The team, RAB LAB, envisions the future of automated mass production using new sustainable materials like 3D-printed concrete. With prefab units and easy assemblies, designers assign part of the authorship to local communities, creating more resilient and flexible urban interventions.
By implementing the innovative low-carbon concrete material, optimizing essential structural forms, and adopting the robotics fabrication system, the 3D printed urban blocks can reduce 30% of overall material waste and increase 80% manufacturing efficiency to achieve the most sustainable and efficient adaptability. The team offers more freedom to bespoke forms and advanced parametric designs by utilizing the technology.
UNIQUE PROPERTIES / PROJECT DESCRIPTION:
This urban furniture prototype can easily adapt to any built environment. Urban Blocks’form can be positioned and combined for different purposes with structural algorithm optimization analysis—single bench, double-side bench, sofas, planters, and variations in-between. The geometry and scale of the mobile units permit easy assemblies to fit the human body. This design aims to empower the communities by prefabricating urban blocks and to open up countless possibilities to populate our public spaces.
OPERATION / FLOW / INTERACTION:
The units are made in factories using sustainable 3D printed concrete with an autonomous robotics fabrication system and transported to sites. People can position them and make different compositions from the blocks to create adaptive urban furniture and landscape elements.
PRODUCTION / REALIZATION TECHNOLOGY:
Prefab Units, Low-Carbon 3D Printed Concrete, Autonomous Manufacture, Robotics fabrication, Modular Design, Bespoke Parametric Design
SPECIFICATIONS / TECHNICAL PROPERTIES:
For each block: 600mm x 750mm x 600mm (being used). When being manufactured/transported, the orientation of the object will be 600mm x 600mm x 750mm to be printed by robots.
CHALLENGE:
The team, RAB LAB, envisions the future of automated mass production using new sustainable materials like 3D-printed concrete. With prefab units and easy assemblies, designers assign part of the authorship to local communities, creating more resilient and flexible urban interventions.
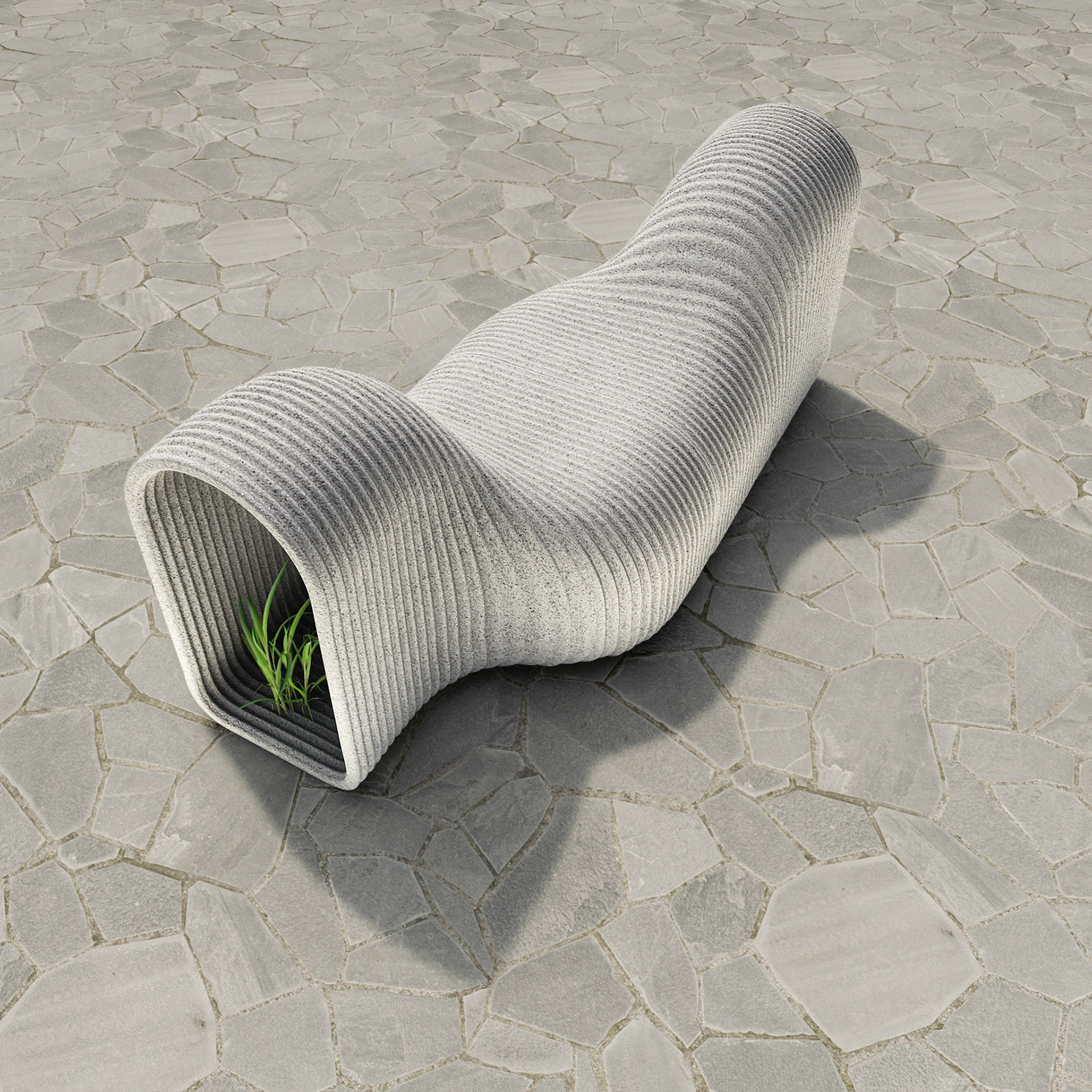
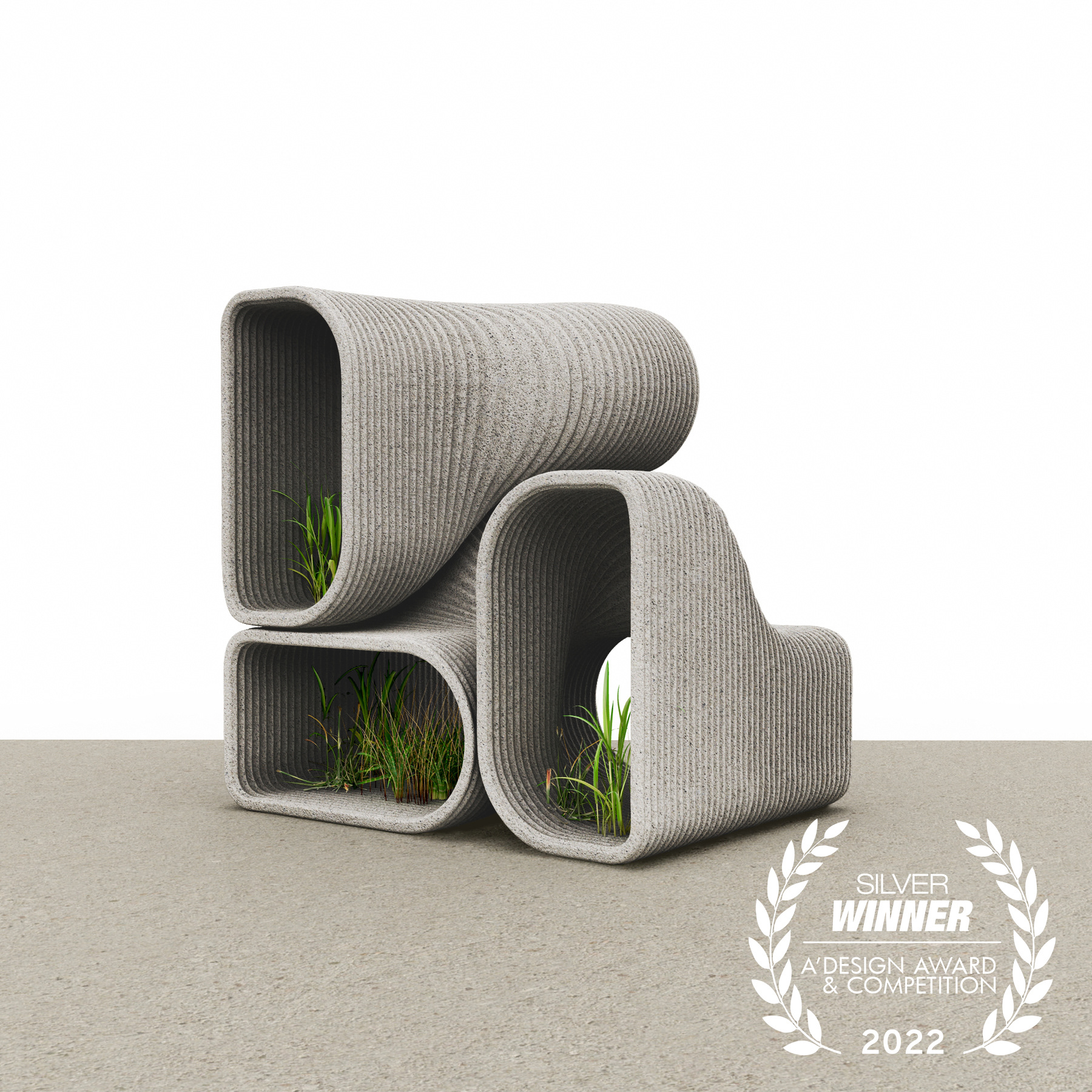
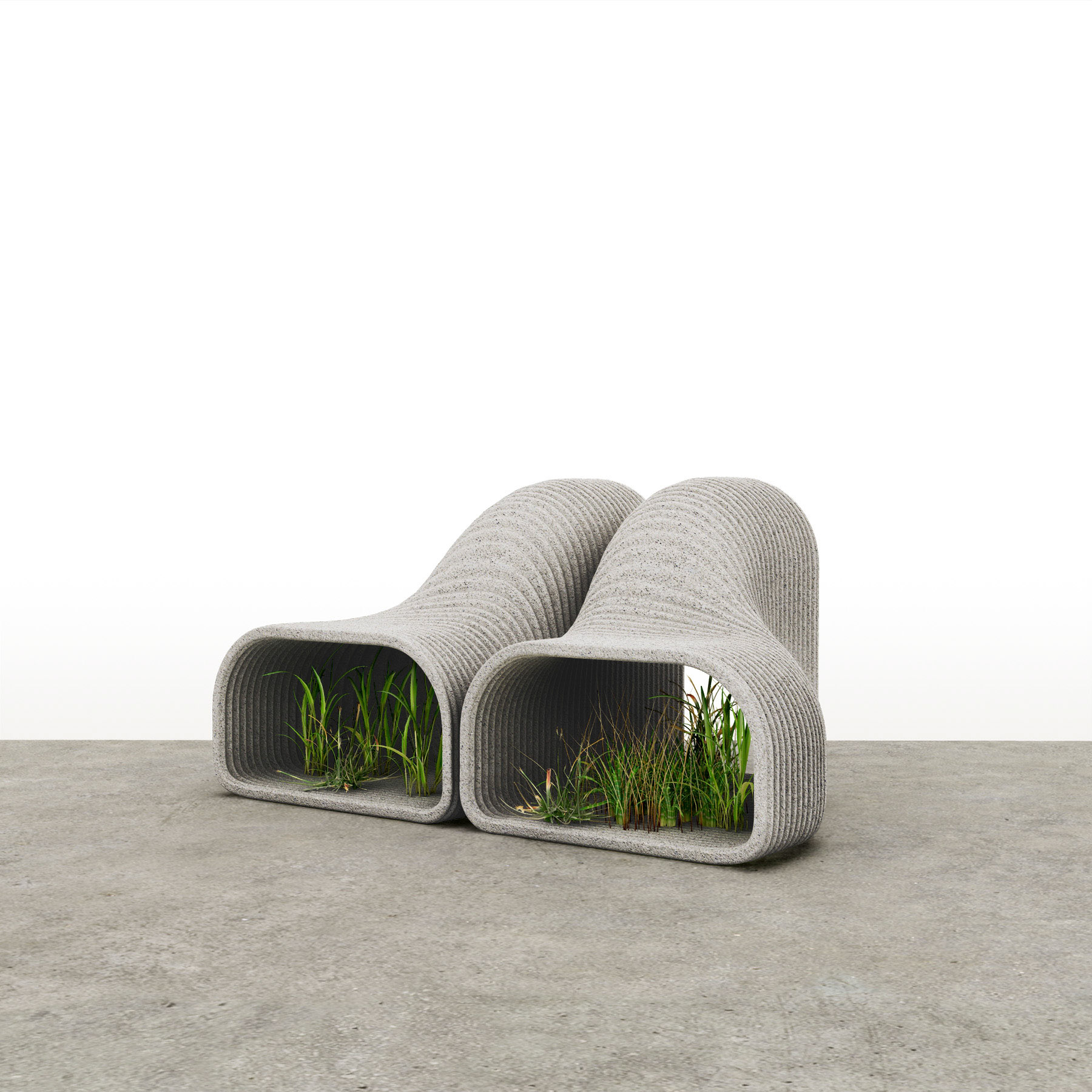
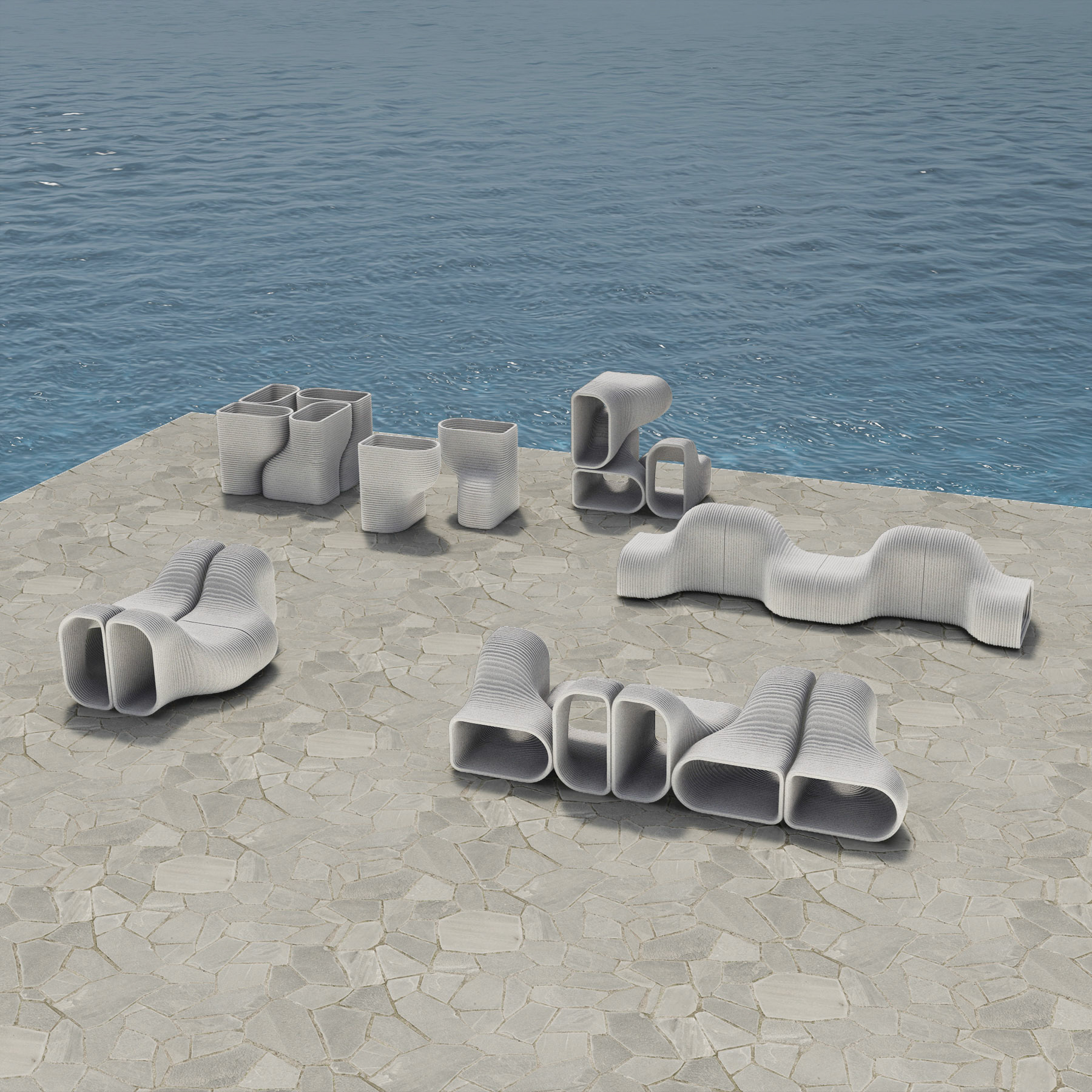
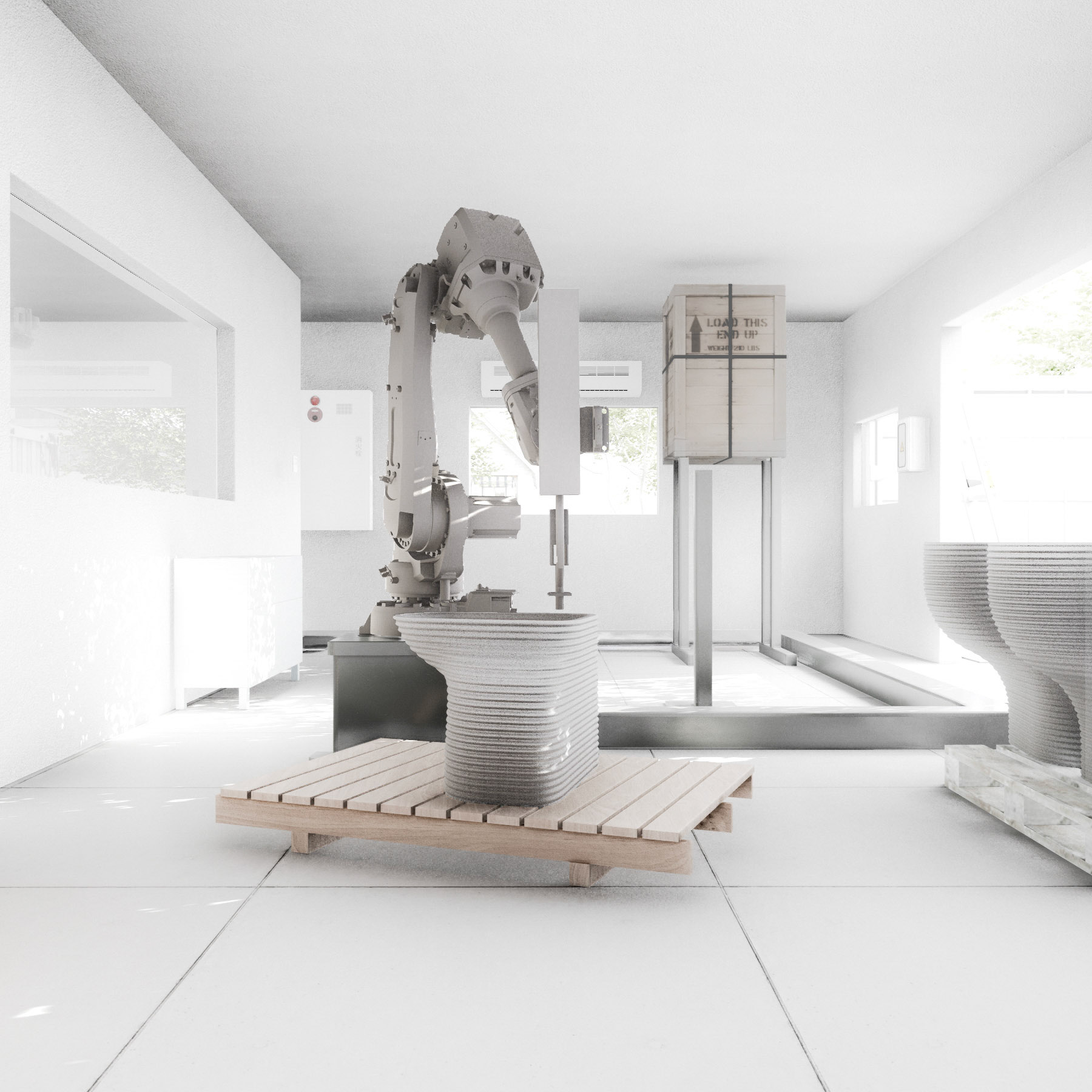